www.przemysl-polska.com
05
'22
Written on Modified on
EMCO: Centrum obróbkowe MEGAMILL zapewnia firmie BYSTRONIC znaczny wzrost wydajności
W branży produkcji obrabiarek jednym z głównych warunków zapewnienia produktywności i gotowości dostaw jest przejrzysta struktura procesu produkcyjnego oparta o precyzyjnie zsynchronizowane sekwencje produkcyjne i niezawodnie funkcjonujące systemy. Można to osiągnąć tylko wtedy, gdy klient i dostawca przyjmą wspólne, zorientowane na cel podejście do projektów łańcucha produkcyjnego.
Tak było właśnie w przypadku realizacji projektu w firmie Bystronic Laser AG z siedzibą w Niederönz w Szwajcarii, polegającego na stworzeniu nowej linii produkcyjnej do obróbki ram maszyn do cięcia laserowego.
Bystronic Laser AG to globalny lider technologiczny w branży obróbki blach, specjalizujący się w systemach cięcia laserowego. Wspólnie z EMCO GmbH z Hallein/Salzburg firma podjęła się zadania całkowitego przeprojektowania procesu obróbki ramy maszyny, tak aby mógł on być realizowany w całości przez frezarkę bramową MEGAMILL firmy EMCO Mecof.
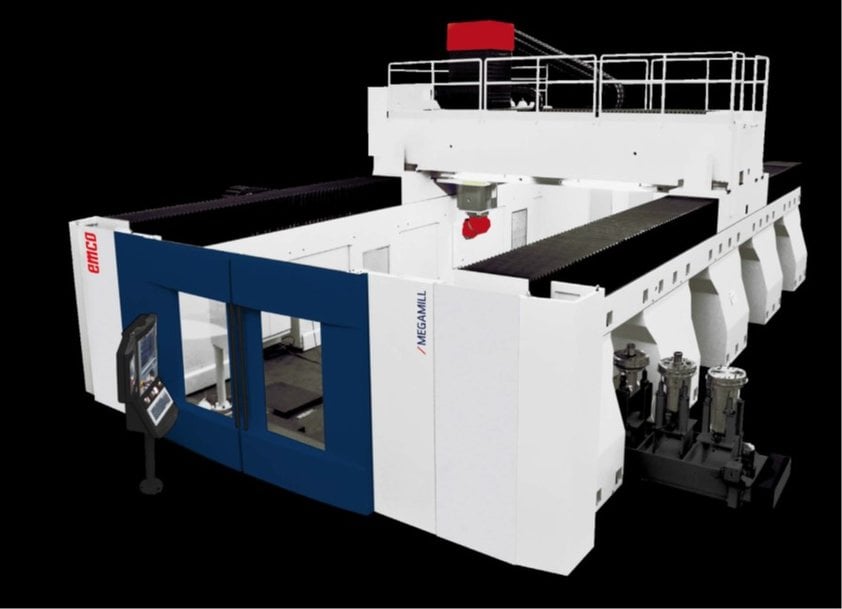
Frezarka portalowa MEGAMILL w trakcie obróbki ciągłej ramy maszyny do cięcia blach
Nowe partnerstwo
- Ilość ram wymagających obróbki wzrosła do tego stopnia, że nasze dotychczasowe moce produkcyjne okazały się niewystarczające. W rezultacie zaczęliśmy szukać nowej maszyny o odpowiedniej wydajności, która spełni wysokie wymagania jakościowe i będzie elastyczna w użytkowaniu - wyjaśnia Raphael Kopp, kierownik produkcji w Bystronic Laser AG.
Raphael Kopp miał ściśle sprecyzowane oczekiwania względem nowej maszyny, do których należały przede wszystkim: wysoka liczba części produkowanych części miesięcznie, doskonała dokładność w
zakresie planowania powierzchni prowadzących ram (płaskość 0,05 mm przy długości prowadnicy 3-4 m) oraz elastyczność umożliwiająca produkcję różnego rodzaju komponentów. Co najważniejsze, stół maszynowy również musiał być wystarczająco duży, ponieważ zespoły systemowe do wycinarek laserowych wymagają znacznej przestrzeni.
Po kontaktach z kilkoma producentami i ocenie wyników testów obróbki, w ciągu niespełna czterech miesięcy stało się jasne, że nową maszyną powinno być centrum obróbkowe MEGAMILL firmy Emco Mecof. W międzyczasie, pracując w ścisłej koordynacji, określono i zweryfikowano kluczowe wymagania i warunki zakupu maszyny oraz zademonstrowano wykonalność projektu.
Raphael Kopp opisuje, w jaki sposób firma podjęła decyzję o zakupie:
- Decydującym czynnikiem była z pewnością możliwość obróbki wahadłowej. Innymi słowy obecnie można zamocować dwa detale na stole maszyny, z których jeden jest obrabiany, a drugi jest równolegle ładowany, wyrównywany i mocowany. Gdy pierwsza część jest skończona, przesuwamy głowicę frezującą na drugą połowę stołu i rozpoczynamy nowe zadanie. Mówiąc kolokwialnie, maszyna zawsze sypie wiórami, co daje nam ogromne oszczędności w czasie produkcji jednej ramy.
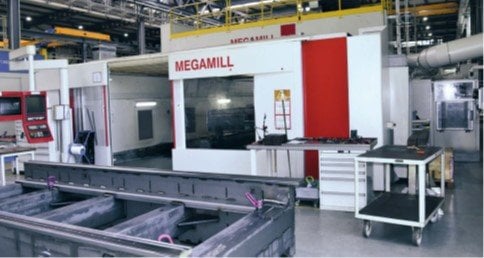
Centrum MEGAMILL zintegrowane z procesem produkcyjnym w Bystronic Laser AG.
Produkcja just-in-time
W firmie Bystronic wydajność produkcji musi spełniać rygorystyczne wymagania. Czas produkcji wycinarki laserowej, od zautomatyzowanego spawania ramy maszyny, poprzez produkcję, malowanie, montaż, kontrolę jakości i uruchomienie, aż do gotowości do wysyłki wynosi 15 dni roboczych.
Produkcja samej ramy maszyny do etapu pomalowanego elementu musi zostać zakończona w ciągu pięciu dni roboczych.
Dzięki centrum MEGAMILL praca odbywa się na trzy zmiany (z jedną zmianą bez nadzoru operatora). Ramy maszyn, które są dostępne w pięciu różnych rozmiarach i ważą ok. 5 t, są wykańczane w czasie od 12 do 16 godzin przy jednej operacji mocowania.
Kompletna obróbka odbywa się w trzech krokach:
/ Obróbka zgrubna: czas produkcji ok. 5 godzin; odprężanie komponentów.
/ Obróbka wstępna: frezowanie wszystkich charakterystycznych konturów, otworów, gwintów itp.
/ Wykańczanie: Precyzyjna obróbka powierzchni prowadzących (płaskość 0,05mm/4m) i wymiarów referencyjnych
Produkcja musi opierać się na niezawodnych procesach, ponieważ przy tak szerokim spektrum działalności firmy awarie, błędy oraz przestoje maszyn dłuższe niż jeden dzień mogą skutkować znacznymi kosztami, a ramy maszyn nie są przechowywane w magazynie po ich wykończeniu.
Z tego powodu kolejne etapy procesu muszą być zawsze realizowane na czas (just-in-time)
MEGAMILL -maszyna oferująca klientom duży potencjał możliwości
MEGAMILL to centrum frezarskie z bramą podwieszaną, idealne do obróbki dużych elementów wykorzystywanych w zastosowaniach, takich jak: produkcja obrabiarek i form, ogólna inżynieria mechaniczna czy lotnictwo. Moduły systemowe maszyny można skonfigurować tak, aby spełniały specyficzne wymagania klienta.
W firmie Bystronic centrum charakteryzuje się długością stołu (oś X) 15 000 mm i osią poprzeczną (oś Gantry-Y) o długości 5000 mm. Z kolei prowadnica Z (RAM) zapewnia przejazd 1750 mm. Z bardzo bogatej oferty głowic frezujących Emco Mecof firma Bystronic wybrała uniwersalną głowicę frezarską. Nie tylko dlatego, że 2-osiowa głowica o momencie obrotowym do 1000 Nm i prędkości 8000 obr./min doskonale spełnia wymagania produkcyjne w zakresie obróbki zgrubnej i wykańczającej, a dzięki kompaktowej konstrukcji może z łatwością dotrzeć do trudno dostępnych konturów ramy.
Dynamiczne pozycjonowanie zapewnia oszczędność czasu w 16-godzinnym cyklu obróbki.
- Szybkie przejazdy w osiach i dynamiczna praca głowicy frezarskiej dają wymierne oszczędności w zakresie czasu obróbki, zwłaszcza gdy trzeba wywiercić ponad 50 otworów w elemencie - podkreśla Raphael Kopp.
Dodatkowo napędy zębate w osiach X i Y, wyposażone w dwa silniki pracujące w konfiguracji master-slave, zwiększają dynamikę procesu. Oczywiście, dużą zaletą jest również realizacja obróbki wahadłowej na stole. Obszary robocze są zaprojektowane tak, aby zapobiegać zagrożeniom bezpieczeństwa, zapewniając, że miejsca, gdzie odpryskują wióry oraz te, do których operator ma dostęp, są bezpiecznie oddzielone. Konfiguracja odbywa się z jednej strony maszyny, podczas gdy głowica frezerska pracuje z drugiej strony. W tym konkretnym zastosowaniu MEGAMILL jest wyposażony w dwa panele sterowania, dzięki czemu operator może interweniować po obu stronach stołu.
Konstrukcja typu «box-in-box» ruchomej poprzecznicy to kolejna mocna strona maszyny. Taka konstrukcja oznacza, że pionowa oś RAM jest mocowana do górnej i dolnej strony belki poprzecznej za pomocą poczwórnych prowadnic liniowych. Tego typu sztywny montaż, optymalizowany metodą MES, gwarantuje zgodność z rygorystycznymi specyfikacjami jakości przedmiotu obrabianego, które są wymagane do wykańczania prowadnic na ramach maszyny do cięcia laserowego.
Maszyna jest całkowicie zamknięta i wyposażona w system ssący.
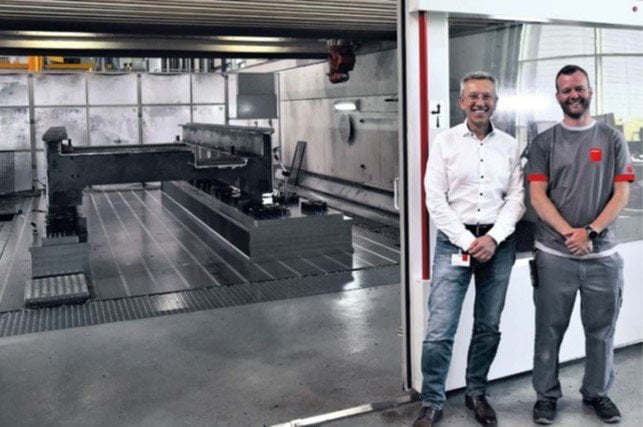
Kluczowymi uczestnikami projektu byli Uwe Urban, kierownik sprzedaży dużych maszyn w Niemczech oraz Raphael Kopp, kierownik produkcji w Bystronic Laser AG. - Teraz, kiedy mamy centrum MEGAMILL, wydajność naszej produkcji osiągnęła nowy poziom - podsumowuje Raphael Kopp.
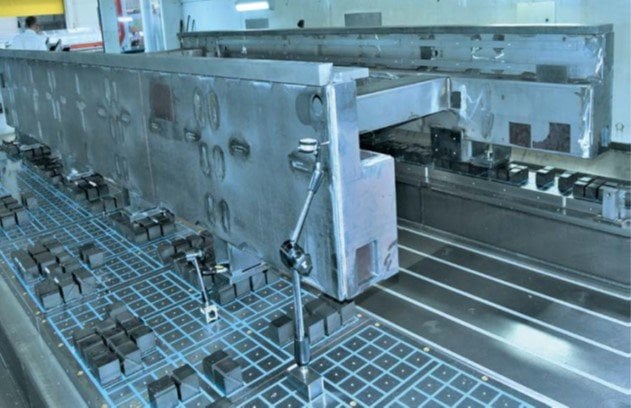
Rama maszyny do cięcia laserowego. Jej pozycjonowanie na stole odbywa się za pomocą mocowania magnetycznego.
Uruchomienie projektu napotyka przeszkody
Planowanie prac projektowych, które rozpoczęły się w 2017 r.: konfiguracja maszyny i jej budowaw zakładzie Emco Mecof w Belforte Monferrato przebiegły bezproblemowo.
Następnie jesienią 2018 r. nadszedł moment dostarczenia centrum obróbkowego do siedziby klienta w Niederönz. Maszyna załadowana na 13 ciężarówek była gotowa do montażu i uruchomienia. Wtedy zaczęły się problemy, bo choć firma Bystronic planowała powstanie nowej hali produkcyjnej, to nie została ona jeszcze ukończona i maszynę trzeba było gdzieś postawić.
Ze względu na utrudniony dostęp, część dachu hali została usunięta, a poprzecznicę ważącą ok. 30 t umieszczono na belkach podłużnych przez otwór w dachu, co wymagało niezwykłej precyzji.
Część maszyny oraz magazynek narzędziowy ze zmieniaczem narzędzi musiały zostać na zewnątrz. Wspólnymi siłami znaleziono rozwiązanie - aby w ogóle oddanie maszyny do użytku było możliwe, wokół jej części, które stały na zewnątrz, zbudowano osobną obudowę. Jednocześnie konieczne okazało się zwiększenie produkcji w zakładzie, więc przyspieszenie odbioru nastąpiło praktycznie w warunkach awaryjnych, co stanowiło spore utrudnienie.
Tego rodzaju niespodziewane sytuacje zdarzają się jednocześnie!
Wydajna 2-osiowa uniwersalna głowica frezarska
Emco Mecof konstruuje głowice obróbcze we własnym zakresie w firmie, co jest ważnym czynnikiem wpływającym na dokładność obróbki. Firma przywiązuje również dużą wagę do dokładności ruchu poprzecznego osi, aby osiągnąć np. praktycznie zerowy luz.
Oprócz szerokiej gamy standardowych głowic, Emco Mecof często opracowuje innowacyjne, dedykowane, specyficzne dla klienta rozwiązania, w szczególności w przypadku serii dużych maszyn portalowych. W serii MEGAMILL głowice obróbkowe ze zintegrowaną osią obrotową i uchylną posiadają bezstopniową regulację oraz sterowanie napędzane silnikiem i są dostępnez motoreduktorem lub szybkoobrotowym napędem wrzeciona. Dzięki inteligentnemu rozmieszczeniu głowicy można ją ustawić tak, aby wykonać podcięcie pod kątem 15° w pozycji poziomej (0°), równolegle do powierzchni stołu. Jest to przydatne, ponieważ eliminuje potrzebę opracowywania ścieżek kompensacji w osiach oraz upraszcza tworzenie programu i generowanie postprocesowe.
Głowice obróbcze są chłodzone przez centralny układ chłodzenia, który zasila również wrzeciono i silniki momentowe.
Dla firmy Bystronic ten poziom kinematyki głowic oznaczał wejście na nowy poziom wydajności. Kinematyka poprzednich maszyn pozwalała na tworzenie programów pracy na panelu sterowania. W przypadku MEGAMILL z głowicą 2-osiową nie było to już wydajne rozwiązanie. Aby stworzyć optymalne programy sekwencyjne, konieczne było wykorzystanie narzędzia CAM. Jego wdrożenie było aktywnie wspierane przez firmę Emco Mecof. Koordynacja transformacji, sekwencje wycofywania głowicy frezarskiej - we wszystkich tych operacjach firma Emco Mecof mogła przekazać klientowi swoje wieloletnie doświadczenie
Optymalizacja obróbki bezobsługowej realizowana poprzez pracę zespołową
Regulacja i późniejsze mocowanie ramy maszyny na stole maszynowym było wcześniej wykonywane ręcznie w standardowy sposób. Obrabianą część kładzie się na powierzchniach nośnych, które są odciśnięte na stole. Procedura ta była czasochłonna, co szybko skłoniło firmę Bystronic do opracowania innego sposobu mocowania. Bazując na zdobytym doświadczeniu z technologią mocowania magnetycznego, która jest również stosowana w fabryce, rozwiązanie to zostało następnie wykorzystane do mocowania ram maszyn w centrum obróbkowym MEGAMILL. Końce części są wstępnie wypoziomowane, dzięki czemu są umieszczane na stole pod kątem.
Następnie docisk magnetyczny regulowany klinami w segmentach zaciskowych przesuwa się do wszystkich punktów podparcia i zaciska część. Eliminuje to czasochłonne, ręczne ustawianie i zaciskanie każdego punktu podparcia.
Ta metoda jest szczególnie wydajna i oszczędna czasowo, gdy w celu wyeliminowania naprężeń wewnętrznych w obrabianej części, zacisk jest przedmuchiwany przez pewien czas po obróbce zgrubnej konturu.
Teraz można to zrobić za pomocą systemu sterowania maszyny, a manualna interwencja nie jest już konieczna. Zamiast tego w systemie sterowania przechowywany jest program sekwencyjny napisany przez Emco Mecof, który można następnie wywołać bezpośrednio za pomocą polecenia M, aby zainicjować proces zwalniania.
Operator nie musi już dochodzić do wszystkich punktów mocowaniaaby zwolnić zaciski, a następnie ponownie je dokręcić do wartości 200 Nm ( dwukrotnie dla każdej części). Oznacza to, że podczas zmiany bez nadzoru operatora realizacja sekwencji jest bardzo dokładna. Praktyczne rozwiązanie zostało również znalezione w przypadku awarii spowodowanej złamaniem wiertła w tym okresie. Maszyna kończy bieżącą operację obróbki, przechodzi w trybie wahadłowym do następnej przygotowanej części i rozpoczyna nowy cykl. Ponowna obróbka przerwanej sekwencji jest następnie wykonywana ręcznie, ponieważ dla firmy Bystronic niezwykle ważne jest, aby każdy przedmiot opuścił zakład prawidłowo obrobiony.
- Bardzo dobra relacja klient-dostawca, którą zbudowaliśmy podczas realizacji projektu, stanowiła istotne wsparcie podczas realizacji naszego nowego pomysłu wdrożenia technologii mocowania magnetycznego. Współpracowaliśmy profesjonalnie i w duchu partnerstwa - Raphael Kopp jest bardzo zadowolony z obecnego procesu produkcyjnego. Od lutego firma Bystronic produkuje części z wykorzystaniem mocowania magnetycznego. Zakład nie doświadczył żadnych problemów i znacznie skrócił czas konfiguracji.
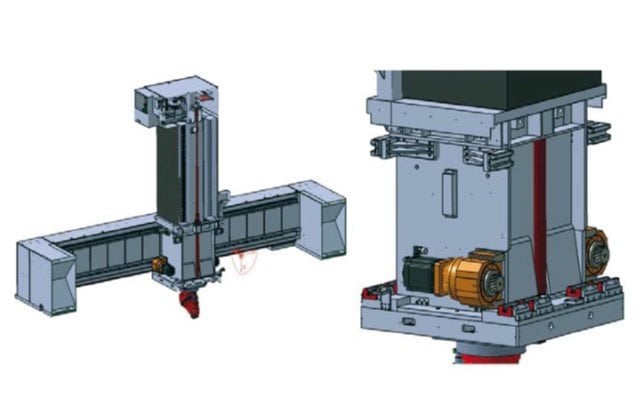
Oś pionowa (RAM) jest zamontowana na ruchomej poprzecznicy w układzie box-in-box, co znacznie zwiększa sztywność
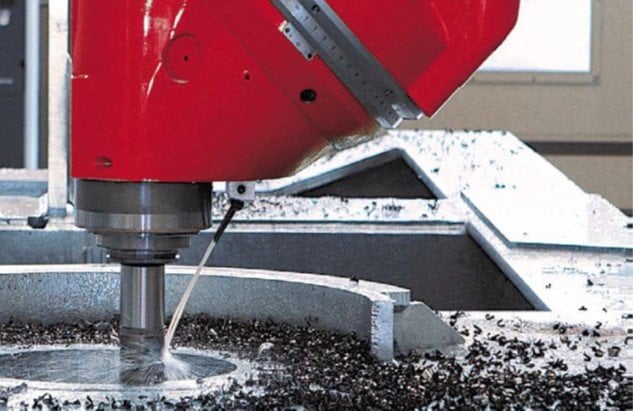
Uniwersalna głowica frezarska z bezstopniową regulacją,ze smarowaniem powietrzno-olejowym, chłodzona wodą. Moc: 38 kW, moment obrotowy: 1000 Nm, max. prędkość: 8000 obr/min, oprawka HSK 100-A
W firmie Bystronic Laser AG przyszłość zaczyna się dziś
Dyrektor zarządzający Fabian Furrer, jest zdecydowanym zwolennikiem strategii, którą firma Bystronic obrała na przyszłość i podkreśla:
- Naszą ambicją jest zachowanie neutralności klimatycznej do 2025 r. i całkowita rezygnacja z paliw kopalnych. Osiągamy to poprzez wyłączenie systemu ogrzewania olejowego i gazowego, oraz wykorzystanie pomp ciepła, których zapotrzebowanie na energię elektryczną pokrywają systemy fotowoltaiczne. Dodatkowo pozyskujemy już energię elektryczną z elektrowni wodnych.
Zastanawiając się nad sposobami oszczędzania zużycia energii, Fabian Furrer ma - jak każdy człowiek - to samo poczucie odpowiedzialności ekologicznej za środowisko, w którym warto żyć.
- Musimy również zoptymalizować nasze produkty pod kątem efektywności energetycznej. Na przykład systemy cięcia laserowego, aby nasi klienci również mogli oszczędzać. W 2018 r. Bystronic zainicjował nową działalność firmy SOLUTION CENTRE, w której opracowywane są rozwiązania umożliwiające cyfrowe połączenie w sieć całego systemu produkcyjnego w zakładzie klienta. Celem wszystkich opracowywanych tu innowacji jest wdrożenie koncepcji SMART FACTORY.
- Klienci coraz częściej proszą o produkcję całkowicie usieciowioną, a my musimy być w stanie im to zapewnić - potwierdza Fabian Furrer.
Właściwa maszyna na właściwym miejscu
Po czterech latach doświadczeń w produkcji ram maszyn z wykorzystaniem centrum MEGAMILL,kadra zarządzająca kwestiami biznesowymi i produkcją mówizgodnie .
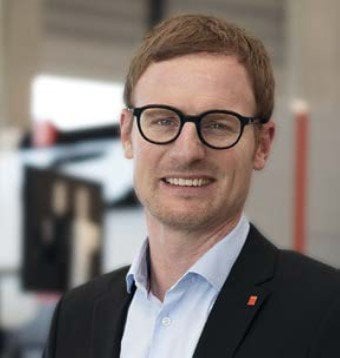
Fabian Furrer, Dyrektor zarządzający Bystronic Laser AG, jednoznacznie stwierdza: „Centrum MEGAMILL precyzyjnie spełnia nasze wymagania, z czego jesteśmy bardzo zadowoleni”
- Obecnie, po czterech latach, możemy bez wątpienia powiedzieć, że MEGAMILL to optymalna maszyna do naszej produkcji - mówi jasno Fabian Furrer.
Podkreśla on w szczególności, że określone wymagania stawiane maszynie zostały w pełni zrealizowane i w przyszłości będzie można wykorzystać maszynę do realizacji nowych pomysłów. W tym zakresie ma już kilka konkretnych koncepcji.
- Zoptymalizowaliśmy czasy produkcji, teraz osiągamy wysoką produktywność i obecnie pracujemy w trybie bez obsługi operatora w 30-40%.
Zamierzamy iść dalej w tym kierunku i rozwijać produkcję bez nadzoru operatora. Z tą maszyną nie powinno być problemu.
Bystronic Laser AG to wiodąca na świecie firma technologiczna w dziedzinie obróbki blach, specjalizująca się w systemach cięcia laserowego.
/ 3500 pracowników na całym świecie
/ Siedziba: Niederönz, Szwajcaria
/40 lokalizacji
/ Sprzedaż netto 2021: 939,3 mln CHF
/ Produkty: Systemy cięcia laserowego, prasy krawędziowe, automatyka, oprogramowanie, serwis.
/ Wycinarka laserowa: Czas produkcji: 15 AT/Mach.
/ Rama maszyny: Czas produkcji 7 AT / rama
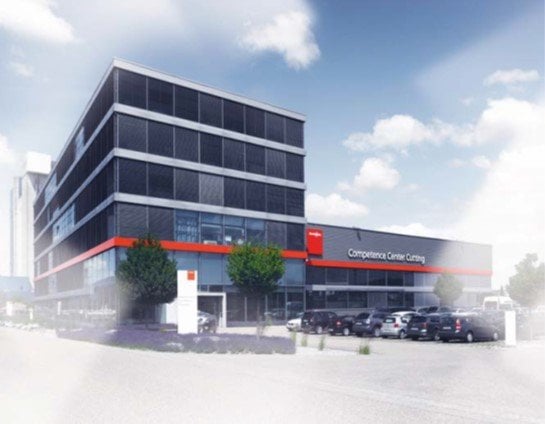
Bystronic Laser AG Industriestrasse 21 / CH-3362
DANE TECHNICZNE
Uniwersalna głowica frezarska z bezstopniowym pozycjonowaniem Moc S1 / S6 38 / 57 kW
Moment obrotowy S1 / S6 1000 / 1550 Nm
Prędkości obrotowe wrzeciona 15 ÷ 6000 obr/min
Opcja 15 ÷ 8000 obr/min
Standardowy uchwyt narzędziowy «ISO 50 DIN 69871 Opcja BIG PLUS
Opcja HSK 100-A DIN 69893"
Elektrowrzeciono 50/63 kW Moc S1/S6 50/63 kW
Moment obrotowy S1 / S6 100 / 125 Nm
Prędkość obrotowa wrzeciona 12000 / 20000 obr./min
Uchwyt narzędziowy HSK 100-A / HSK 63-A
Elektrowrzeciono 42 / 55 kW Moc S1 / S6 42 / 55 kW
Moment obrotowy S1 / S6 67 / 87,5 Nm
Prędkość obrotowa wrzeciona 24000 obr./min
Uchwyt narzędziowy HSK 63-A
Elektrowrzeciono 45 / 58 kW Moc S1 / S6 45 / 58 kW
Moment obrotowy S1 / S6 300 / 372 Nm
Prędkości wrzeciona 12000 obr./min
Uchwyt narzędziowy HSK 100-A
Elektrowrzeciono 70 / 86 kW Moc S1 / S6 70 / 86 kW
Moment obrotowy S1 / S6 160 / 220 Nm
Prędkości wrzeciona 15000 obr./min
Uchwyt narzędziowy HSK 100-A
Osie liniowe
Przesuw osi wzdłużnej 7500mm i więcej (w krokach co 2500 mm)
Przesuw osi poprzecznej 4000 - 5000 - 6000 - 7000 mm
Przesuw osi pionowej 1500 - 2000 - 2500 mm
Prędkość posuwu 30 m/min
Przekrój prowadnic pionowych RAM 550 x 640 mm
Sterowanie CNC Heidenhain TNC 640 HSCI; Siemens 840D sl; Sinumerik ONE
Napęd wrzeciona
Standardowo 40 kW / 1200 Nm
Opcja 50 kW / 1500 Nm (S1), 61 kW / 1800 Nm (S6)
Układ chłodzenia przedmiotu obrabianego/narzędzia
Niskie ciśnienie 28 l/min, 6 bar
Wysokie ciśnienie (przez wrzeciono) 20 l/min, 20 / 40 / 60 bar
Opcje standardowe
Uniwersalna głowica frezarska 5-osiowa do obróbki ciągłej 6000 obr/min
Głowica frezarska z wrzecionem do obróbki pozaosiowej 3000 obr/min
Uniwersalna głowica z silnikami momentowymi i elektrowrzecionem 12000 / 20000 / 24000 obr./min 5-osiowa głowica frezarska widłowa z silnikami momentowymi i elektrowrzecionem 12000 / 15000 / 20000 / 24000 obr./min
Automatyczny magazyn narzędzi 48/64/96/128 oprawek
Automatyczny magazynek głowic 2/3 oprawki