www.przemysl-polska.com
02
'19
Written on Modified on
Możliwość różnorodnego wyboru innowacyjnych materiałów o wysokiej jakości zapewnia optymalną wydajność
Wybierając odpowiedni materiał, użytkownicy powinni zawsze brać pod uwagę zakres zastosowań. Marcus Schneck - CEO norelem wyjaśnia, dlaczego stosowanie części roboczych wykonanych z wysokiej jakości materiałów ma kluczowe znaczenie dla zapewnienia niezawodności i stabilności używanych komponentów i wytwarzanych produktów.
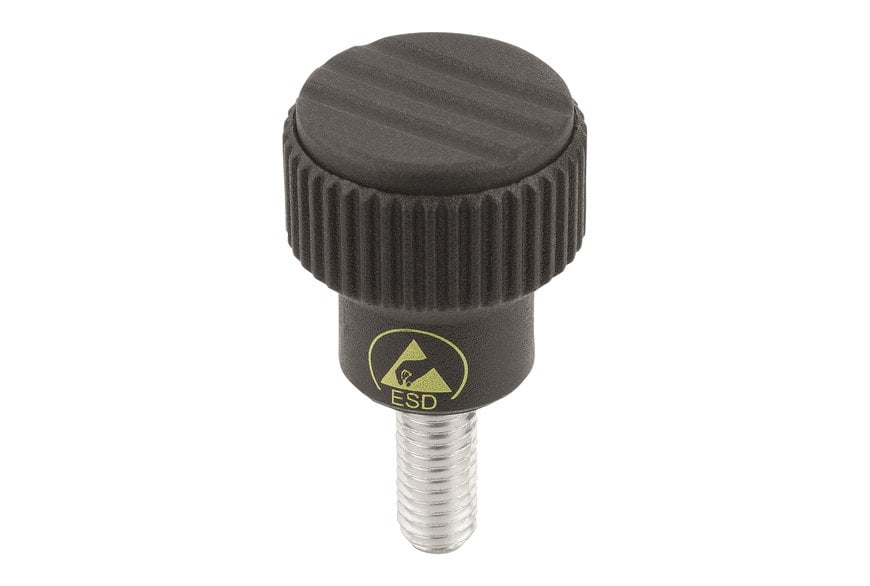
Rozglądając się po hali produkcyjnej z pewnością dostrzeżemy liczne, metalicznie połyskujące elementy maszyn i wyposażenia. Należy jednak podkreślić, że innowacje w zakresie tworzyw sztucznych i możliwości procesowych w połączeniu ze zmianami wymagań w branży przemysłowej zmniejszyły różnice techniczne i wydajnościowe, które kiedyś były zauważalne pomiędzy metalami a tworzywami sztucznymi.
Rodzaj wybieranych materiałów jest naturalnie ważnym czynnikiem, który należy wziąć pod uwagę podczas użytkowania komponentów standardowych i roboczych. Właściwy ich wybór gwarantuje bowiem uzyskanie wysokiej jakości, trwałych produktów, a odpowiednie wykończenie i obróbka powierzchni zapewniają, że komponenty, takie jak uchwyty czy pokrętła są także atrakcyjne wizualnie.
Materiały kompozytowe, takie jak wzmacniany włóknem szklanym poliftalamid PPA (Polyphthalamide), również można wykorzystywać z powodzeniem w sektorze produkcyjnym i konstrukcyjnym ze względu na ich lekkość, relatywną sztywność, wytrzymałości i trwałość. Popularność tych materiałów stale się zwiększa - globalny rynek materiałów kompozytowych wzrasta ok. 5% rocznie, natomiast popyt na włókna węglowe rośnie o 12% w skali roku.
Odpowiedni materiał do każdej aplikacji
Jest oczywiste, że podczas wyboru komponentów standardowych i materiałów, z których są wykonane należy wziąć pod uwagę szereg czynników. Ważnymi kryteriami wyboru może być niemal wszystko: od odporności na rozciąganie i korozję, poprzez zakres temperatury pracy, aż do odporności chemicznej. Uwzględnienie tych elementów, jak również środowiska pracy, w którym materiał będzie używany, pomoże wybrać materiał dopasowany do specyfiki konkretnej aplikacji.
Najbardziej popularnymi materiałami stosowanymi w branży produkcyjnej i konstrukcyjnej są tworzywa sztuczne, stal, aluminium, żeliwo, metale nieżelazne i stale nierdzewne.
Zastosowanie plastików w branży konstrukcyjnej pokazało, że odchodzenie od materiałów metalowych na rzecz tworzyw sztucznych może zapewnić oszczędności od 25 do 50% ze względu na wyeliminowanie konieczności stosowania elementów złącznych i prac montażowych. Plastiki mogą być używane w wielu aplikacjach, takich jak prasy hydrauliczne, granulatory czy linie do wytłaczania tworzyw sztucznych.
Jednocześnie wstawki, takie jak tulejki czy trzpienie gwintowane, są wykonywane ze stali, stali nierdzewnych lub mosiądzu, oferujących wysoką odporność udarową, co sprawia, że są to pożądane materiały do stosowania w maszynach. Połączenie plastików i metali może być bardzo korzystne, jeśli stosuje się je łącznie, wykorzystując najlepsze cechy obu materiałów.
W przypadku uchwytów pałąkowych, rurowych i kasetowych, jak również dźwigni zaciskowych i nastawnych, proporcje użycia komponentów metalowych są nieco wyższe. Z kolei pokrętła radełkowane, krzyżowe i gwiaździste są wykonane głównie z plastików ze względu na przyjazne dla użytkowników właściwości tych materiałów.
Wyładowania elektryczne, tarcie i wysokie temperatury to trzy wyzwania w branży produkcyjnej i konstrukcyjnej, które wymagają zastosowania specyficznych materiałów w celu zapewnienia bezpiecznego i wydajnego działania maszyn.
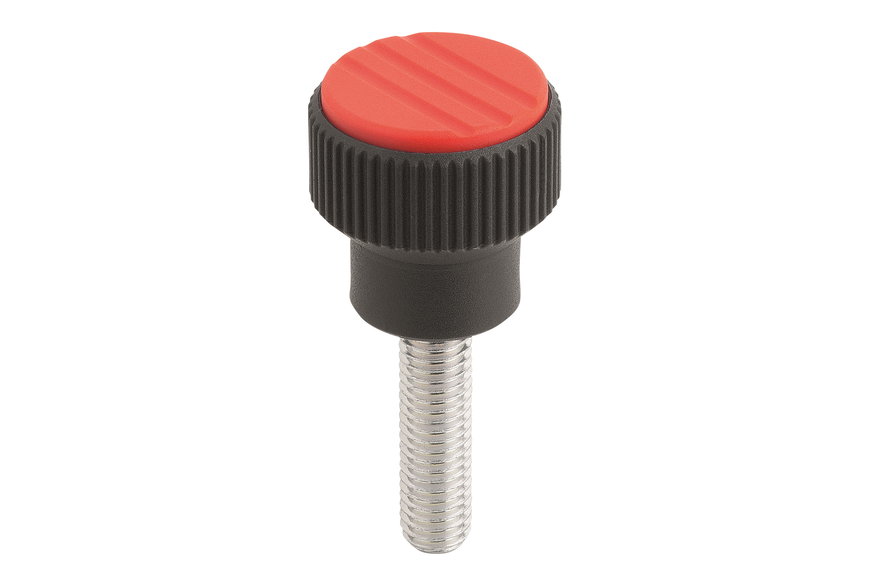
Specjalne aplikacje wymagają specjalnych materiałów - dobrym tego przykładem są antystatyczne części robocze. Są one wykonane z elektrycznie przewodzącego plastiku, co zapobiega wyładowaniom elektrostatycznym, które mogą negatywnie wpływać na wrażliwe komponenty elektroniczne.
Komponenty wykonane z antystatycznego termoplastu, spełniające normę DIN EN 61340-5-1, mogą być stosowane w strefach ochronnych przed ESD (Electrostatic Discharge, wyładowania elektrostatyczne). Tego typu produkty są używane również w urządzeniach, komponentach i systemach ochronnych w obszarach o wysokim zagrożeniu wybuchem.
Dobrane właściwie materiały i izolatory są w stanie razem wyeliminować wyładowania elektrostatyczne, zapewniając bezpieczne i pewne środowisko pracy oraz ograniczając jednocześnie konieczność konserwacji maszyn na dalszych sekcjach linii produkcyjnej.
Wyładowania elektrostatyczne zdarzają się całkiem często podczas produkcji, montażu czy transportu, a antystatyczne elementy robocze stanowią rozwiązanie tego problemu. Kluczowe dla bezpieczeństwa maszyn i ludzi jest zapewnienie regularnego testowania komponentów pod kątem przewodności elektrycznej w zgodzie z surowymi standardami oraz jednoznaczna identyfikacja zagrożeń za pomocą żółtego logo ESD.
Jak zapewnić odporność na wysokie temperatury?
Wzmocniony włóknem szklanym poliftalamid PPA - materiał kompozytowy, który w przeciwieństwie do standardowych tworzyw sztucznych charakteryzuje się wyjątkową stabilnością wymiarową - jest powszechnie wybierany do zastosowań w strefach występowania wysokich temperatur. Komponenty wykonane z tego materiału wytrzymują temperaturę do 150°C, a krótkotrwale nawet do 250°C.
Produkty te znajdują zastosowanie w licznych branżach, takich jak technologia medyczna, gdzie komponenty muszą wytrzymywać sterylizację parą. Stanowią również dobry wybór do wszystkich obszarów konstrukcji wyposażenia, w których panują wysokie temperatury otoczenia.
Komponenty wykonane z termoplastu wzmacnianego włóknem szklanym, stosowane głównie do uchwytów roboczych, zapewniają bardzo wysoki komfort chwytania, nawet w strefach zawilgoconych. Wybór właściwego materiału jest kluczowy także dla bezpieczeństwa pracowników, gwarantując, że wykorzystane materiały nie zatrzymują ciepła i nie poparzą/zranią pracownika w trakcie obsługi maszyny.
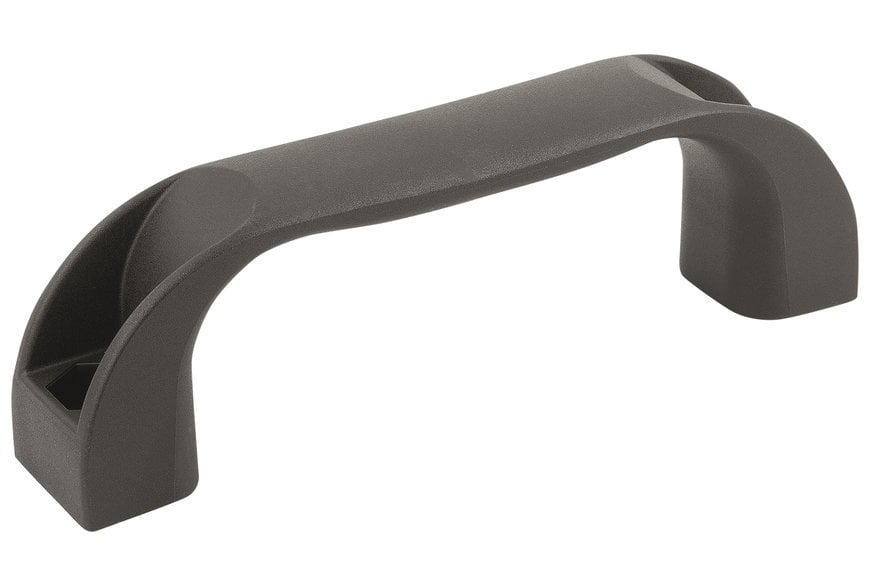
Przy szerokim zakresie wyboru materiałów w branży, istotny jest właściwy ich dobór do odpowiedniej aplikacji, w celu zapewnienia płynnej pracy maszyn i komponentów.
W przypadku pracy w obszarach o wysokim tarciu ( np. koła zębate) poliacetal gwarantuje wysoką twardość i niski współczynnik tarcia, niemniej jednak poliketon oferuje dużo dłuższy okres eksploatacji i optymalne przeniesienie mocy. Ze względu na wyjątkowo wysoką odporność na ścieranie i bardzo dobre właściwości trybologiczne, znacznie zredukowana została również podatność na uszkodzenia/złamania zębów.
Zastosowanie ołowianych lub miedzianych powierzchni nośnych również ogranicza ryzyko tarcia pomiędzy komponentami i częściami maszyn, tak samo jak właściwe smarowanie zmniejsza tarcie i zużycie elementów.
Ponieważ przemysł wypełnia lukę pomiędzy stosowaniem metali i tworzyw sztucznych, inżynierowie i producenci muszą podejmować decyzję, który materiał jest najlepszy do konkretnych zastosowań.
Stosowanie części z tworzyw sztucznych daje producentom większą swobodę i elastyczność, włączając w to szerszy wybór materiałów. Oczywiście metale mają ustaloną reputację, jako solidne i trwałe materiały, ale plastiki z pewnością mogą być tak dobre, jak ich metalowe odpowiedniki, szybko stając się przydatnym materiałem ze względu na swoją lekkość i elastyczność.
Więcej informacji można znaleźć na stronie: www.norelem.pl