www.przemysl-polska.com
03
'18
Written on Modified on
Realia współczesnej ekonomiki produkcji
Wydziały produkcyjne zajmujące się obróbką starają się wytworzyć pewną liczbę części o określonej jakości, w określonym czasie i w określonej cenie. Konsekwentna realizacja tych celów wymaga kontroli niezliczonych czynników, takich jak parametry skrawania, koszty narzędzi i czasy przezbrojeń, eksploatacja obrabiarek, koszty manipulacji materiałami oraz koszty materiałowe i koszty pracy.
Ekonomika produkcji to sztuka znalezienia równowagi między czynnikami procesu w celu osiągnięcia żądanych wyników. Przez ponad dwa wieki historii obróbki skrawaniem liczba czynników odgrywających rolę w ekonomice produkcji zwiększyła się wielokrotnie. Produkcja ewoluowała od poziomu rzemiosła produkującego pojedyncze elementy do poziomu masowej produkcji standardowych części za pomocą obrabiarek. Udoskonalenie metod produkcji zapoczątkowało drugą generację produkcji masowej z liniami produkcyjnymi oraz coraz większą wydajnością wytwarzania identycznych części: mowa o masowej produkcji mało zróżnicowanego asortymentu (HVLM). Pojawienie się obrabiarek CNC i robotów umożliwiło uzyskanie wydajności, która rozpoczęła trzecią generację produkcji masowej. Ostatnio, dzięki zastosowaniu technik cyfrowych do programowania, sterowania obrabiarkami i obsługi obrabianych elementów, narodziła się czwarta generacja produkcji, znana jako Przemysł 4.0, w której możliwe jest opłacalne wytwarzanie zróżnicowanych produktów w niewielkich ilościach (HMLV).
HQ_POS_Manufacturing_Process_Evolution.jpg
Skuteczne przejście z produkcji HVLM na HMLV wymaga od producentów znajomości zmieniających się i coraz liczniejszych okoliczności ekonomiki produkcji oraz wykorzystania dostępnych informacji i technologii do analizy działań, która pozwoliłaby osiągnąć zakładane cele. Kluczowym elementem projektu transformacji jest odrzucenie nadmiernie uproszczonych przekonań i praktyk oraz ujawnienie ukrytych kosztów, które przy próbie maksymalizacji produktywności mogą stać się przeszkodą.
Duża ilość, małe zróżnicowanie, prosty rachunek?
Standaryzację procesów obróbki skrawaniem opracowano w XIX wieku w celu przyspieszenia produkcji identycznych produktów o wymiennych częściach. Przemysł motoryzacyjny maksymalnie dopracował produkcję typu HVLM, wprowadzając linie transportowe i inne metody umożliwiające wytwarzanie setek tysięcy lub milionów tej samej części przez lata.
Długofalowy charakter produkcji HVLM umożliwia producentom dostrojenie szeregu czynników procesu i zapewnienie maksymalnej wydajności, powtarzalności oraz niskiego kosztu. Zminimalizowaniu zmienności sprzyjają także technologie pomocnicze, takie jak zmieniacze narzędzi i palet. Zakłada się, że operacja przebiega bez zakłóceń i zapewnia 100% wydajności, jeśli koszty są przewidywalne, nie występują nieplanowane przestoje, odrzuty ani konieczność przeróbek i nie ma potrzeby wykonywania czynności dodatkowych, takich jak usuwanie zadziorów.
Przyjmuje się między innymi, że koszt narzędzia stanowi zazwyczaj około trzech procent całkowitych kosztów produkcji. Trzy procent to wygodny punkt odniesienia, jednak ta wartość rzadko bywa prawidłowa. Dużą rolę gra tu na przykład charakterystyka obróbki danego elementu: zamiana stali na tytan może pięciokrotnie zwiększyć zużycie narzędzi. Inne parametry pozostają bez zmian, ale z trzech procent robi się piętnaście.
Skupienie się wyłącznie na czasie użycia narzędzia skutkuje zaniedbaniem innych czynników, takich jak czas bezczynności podczas jego wymiany. Takie podejście to ucieczka od rzeczywistości. Producenci powinni zrozumieć, że liczy się także czas obróbki, konfiguracji, wymiany narzędzi, załadunku i rozładunku oraz inne czynniki, które na siebie nawzajem oddziałują.
W uproszczonym przykładzie nieprzewidzianej interakcji czynników procesu produkcyjnego warsztat obrabia część, która wymaga dwóch minut czasu obróbki i łącznie dwóch minut na załadowanie i rozładunek. Indeksowanie narzędzia trwa jedną minutę, a jego trwałość to pięć elementów obrabianych. W ten sposób indeksowanie narzędzia zajmuje 0,2 minuty na jedną część. Ponieważ każda część wymaga 4,2 minuty czasu obróbki, na godzinę można wyprodukować nieco ponad 14 sztuk. Każde narzędzie kosztuje 15 euro, co przy trwałości 5 przedmiotów obrabianych daje 2,8 narzędzia (42 euro) potrzebnego do wytworzenia 14 przedmiotów obrabianych. Koszt pracy maszyny wynosi 50 euro na godzinę. Podsumowując, koszty produkcji 14 przedmiotów obrabianych na godzinę wynoszą 92 euro.
Następnie, próbując zwiększyć tempo i wydajność, warsztat zwiększa prędkość skrawania o 10 procent. Skraca to czas skrawania o 10% (do 1,8 minuty), ale także obniża trwałość narzędzia mniej więcej o połowę, co oznacza, że jedno ostrze będzie produkować tylko dwa i pół przedmiotu obrabianego, zanim konieczne będzie indeksowanie. Czas indeksowania narzędzia wciąż wynosi jedną minutę, a załadunek/rozładunek przedmiotu obrabianego trwa dwie minuty. Czas produkcji jednego przedmiotu obrabianego to wciąż 4,2 minuty (1,8 minuty na obróbkę, 2 minuty na manipulację i 0,4 minuty na indeksowanie narzędzia) lub 14 przedmiotów obrabianych na godzinę. Maszyny i koszty narzędziowe są takie same, ale teraz do pracy przez godzinę potrzeba 5,6 narzędzia (koszt narzędzi wynosi 84 euro). Pomimo wszelkich starań, aby przyspieszyć wydajność, czas wyprodukowania 14 przedmiotów jest identyczny, a koszt rośnie z 92 euro do 134 euro.
W takim przypadku zwiększenie prędkości skrawania nie powoduje wzrostu wydajności. Zmiana czasu skrawania wpływa na inne czynniki związane z obróbką — w tym przykładzie jest to trwałość narzędzia oraz czas indeksowania. W związku z tym warsztat musi starannie rozważyć wszystkie konsekwencje zmian procesów.
Ukryte koszty mogą także wynikać z realizacji poszczególnych etapów procesu. W przypadku wielu warsztatów książkowym przykładem może być czas spędzony na indeksowaniu płytek. Limit może wynosić jedną minutę, jednakże pomiar wykonany na hali produkcyjnej może dać wynik dwóch, trzech lub dziesięciu minut, co oznacza różnicę od 60 do 600 sekund.
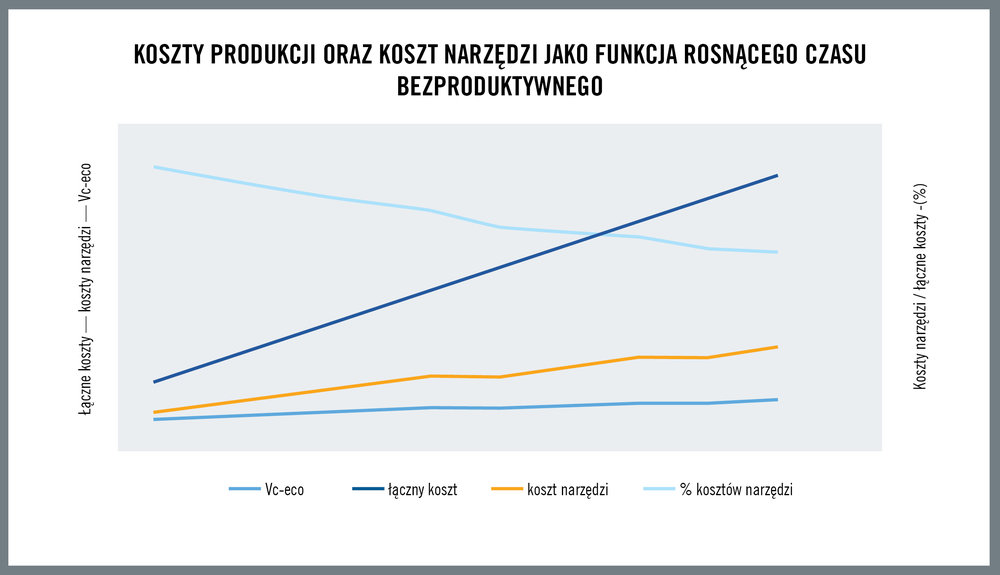
HQ_ILL_Production_Cost_And_Tooling_As_A_Function_Of_Increasing_Idle_Times.jpg
Ilustracja 2
Mała ilość, duże zróżnicowanie, skomplikowane zagadnienia
Presja globalnej konkurencji skłania dziś producentów do wytwarzania różnych wersji produktów, które będą odpowiadały potrzebom mniejszych grup użytkowników. Zaawansowana technologia umożliwia szybką zmianę projektów części i programów obróbki, a także umożliwia łatwe śledzenie wersji i zapasów magazynowych. W rezultacie nastąpiło przejście na produkcję w trybie HMLV, a postępy, jakie dokonały się w tej dziedzinie, umożliwiają dziś wydajne wytwarzanie serii liczących mniej niż 10 produktów lub wręcz pojedynczych części.
Wydłużony horyzont czasowy produkcji HVLM umożliwia celowe planowanie i dostosowanie czynników procesu. Planowanie jest inne w przypadku produkcji HMLV. Skomputeryzowane technologie inżynierskie i magazynowe umożliwiają szybką zmianę typu produktu i wydajności, jednak wiąże się to z większym skomplikowaniem procesów planowania HMLV i koniecznością ich dynamicznego dostosowywania. Po zamówieniu opiewającym na dziesięć części mogą następować partie po dwa elementy lub pięć lub nawet partie obejmujące pojedyncze sztuki różnych rodzajów produktów. Obrabianym materiałem może być raz stal, a po chwili tytan lub aluminium, zaś geometria może zmieniać się z prostej w złożoną. Brak jest wystarczającej ilości czasu, aby określić trwałość narzędzia poprzez próby.
Zarządzanie trwałością narzędzia przy produkcji HMLV polega zazwyczaj na zachowawczym oszacowaniu jego trwałości. Ponadto dla bezpieczeństwa narzędzia wymienia się na nowe przed każdą partią produkcyjną, na długo przed osiągnięciem przez nie kresu przydatności. Czas skrawania jest tylko jednym z elementów całościowego obrazu. W produkcji HMLV czas potrzebny na obsługę różnych obrabianych przedmiotów i mocowań, zmianę narzędzi i indeksowanie płytek często jest dłuższy niż rzeczywisty czas skrawania. Także oprzyrządowanie, narzędzie skrawające, czas bezczynności, robocizna oraz własności obrabianego materiału mogą generować ukryte koszty. W najnowszym ujęciu w ekonomice produkcji uwzględnia się koszty narzędzia, obrabianego materiału, sprzętu oraz produkcji, a także koszty sprzętowe przestojów, wynagrodzenia i koszty konserwacji.
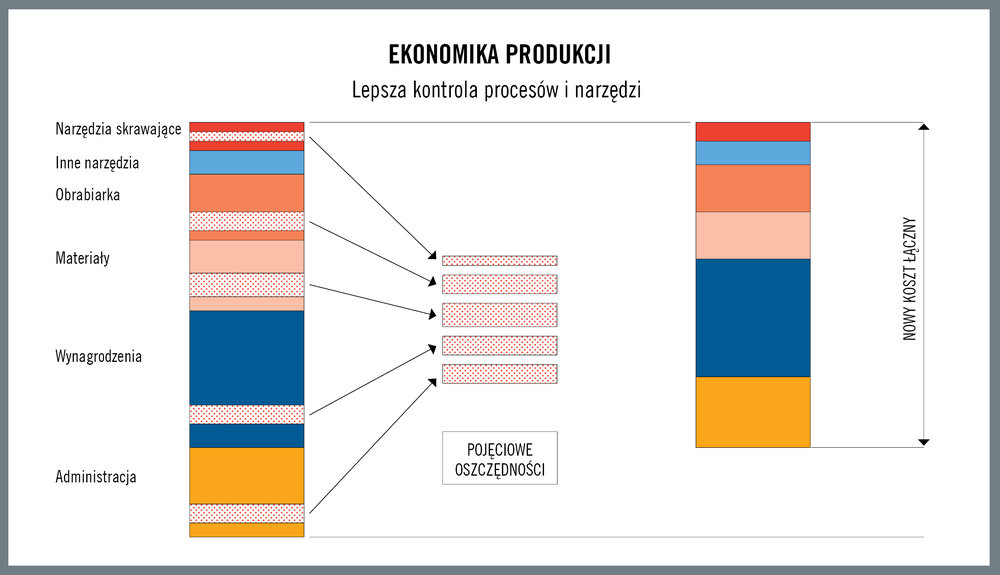
HQ_ILL_Production_Economics
Ilustracja 3
Szybko zmieniające się wymagania produkcji HMLV powodują, że trudno uzyskać wysoką wydajność. W przypadku długoterminowej produkcji HVLM metoda testów i dostrajania może przynieść wydajność rzędu dziewięćdziesięciu kilku procent. Z kolei w przypadku produkcji HMLV sytuacja może być zero-jedynkowa. Udana produkcja partii obejmującej jedną część oznacza 100-procentowy sukces, ale kiedy część nie spełnia wymogów lub zostanie zniszczona, wydajność wynosi zero. Wymagania dotyczące jakości oraz odpowiedniego stosunku kosztów i czasu pozostają takie same, ale najważniejszym wymogiem staje się powodzenie w pierwszym podejściu. W takim przypadku największy nacisk należy być może położyć na unikanie uszkodzenia narzędzia. Jedną z zalet takiej sytuacji jest to, że przy krótkich seriach zużycie narzędzia nie jest problemem i warsztat może, w granicach rozsądku, zastosować bardziej agresywne i produktywne parametry skrawania.
Wiąże się z tym konieczność określania, kiedy należy indeksować narzędzie. Zbyt długie oczekiwanie może spowodować uszkodzenie narzędzia i przerwę w produkcji, a w najgorszym przypadku uszkodzenie obrabianego elementu. Z drugiej strony zbyt częsta wymiana narzędzi generuje dodatkowe koszty poprzez zwiększenie kosztów narzędziowych i stratę czasu spowodowaną zatrzymaniem maszyn i indeksowaniem. Określenie właściwego momentu wymiany narzędzia wymaga sprawdzenia, jak ma się ona do całego systemu obróbki, a także utworzenia protokołu wymiany narzędzi, a następnie jego rygorystycznego przestrzegania.
Wnioski
Relacje między poszczególnymi czynnikami w systemie obróbki metali skrawaniem są wielostronne. Zmiana warunków skrawania, obrabianych materiałów lub wielkości produkcji będzie mieć wpływ na trwałość narzędzia, jak również wiele innych aspektów systemu. Wyzwaniem z punktu widzenia ekonomiki produkcji w zakładzie produkcyjnym jest zrozumienie tych związków i opracowanie strategii, która umożliwi pracę z nimi. Niestety, nie każdy pracownik warsztatu może być profesorem matematyki, a poza tym brakuje czasu na dogłębną analizę powiązań. W rezultacie dostawcy oferują analizy procesu i usługi zarządzania (patrz pasek boczny), które zapewniają producentom kompleksowy obraz konkretnych operacji i dostarczają wskazówek w zakresie sposobów maksymalizowania wydajności oraz optymalizacji działań w kontekście ekonomiki.
Właściciele warsztatów często narzekają, że mimo licznych zleceń i klientów, którzy płacą, wciąż notują straty finansowe. Rozwiązaniem tych problemów może być zapoznanie się z realiami współczesnej ekonomiki produkcji i eliminacja kosztów,
które pozostają ukryte lub są lekceważone. W ten sposób można osiągnąć maksymalną opłacalność produkcji.
Pasek boczny
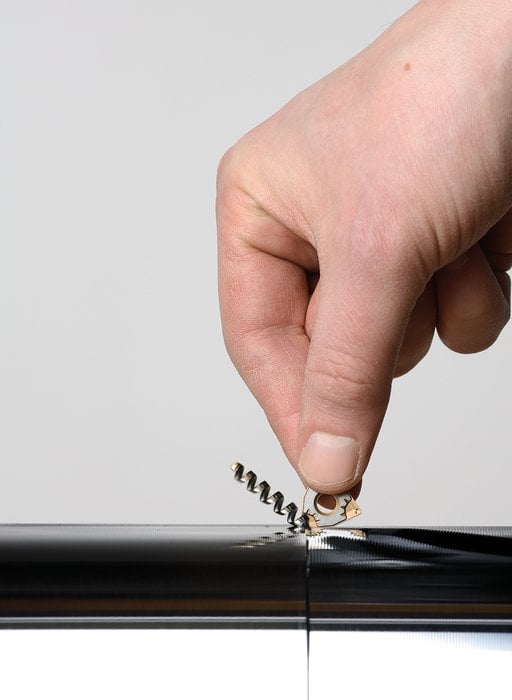
HQ_IMG_Duratomic_Chip.jpg
Ilustracja 4
Zautomatyzowana analiza
Od zarania produkcji masowej liczba czynników mających wpływ na wydajność i koszty produkcji zwiększyła się wielokrotnie. Relacje pomiędzy elementami systemów produkcyjnych stały się bardziej złożone, podobnie jak same operacje obróbki i maszyny. Żaden z elementów nie istnieje niezależnie; przykładowo, zmiana wymogów w zakresie wielkości produkcji będzie miała wpływ na koszty narzędzi, sprzętu, konserwacji, pracy i nie tylko.
Określanie liczby istotnych czynników oraz ich wzajemnych relacji jest poważnym wyzwaniem. Złożoność wymaga systematycznego podejścia do kwestii pomiarów, sterowania oraz zarządzania procesami produkcyjnymi.
System analizy kosztów wydajności (PCA) firmy Seco bada cały proces produkcyjny w celu określenia sposobów na obniżenie kosztów i zwiększenie produktywności. System powstał w oparciu o wiedzę i doświadczenie, które firma Seco przez dziesięciolecia gromadziła na całym świecie. Seco stosuje tę wiedzę w połączeniu z zaawansowanymi analizami komputerowymi i algorytmami. Używane są między innymi techniki symulacji Monte Carlo, które umożliwiają automatyzację modelowania kosztów.
Analizę PCA przeprowadza wykwalifikowany przedstawiciel Seco. Ocenie podlegają wszystkie narzędzia i technologie używane w procesie. Następnie powstaje kompleksowy raport, który zawiera zarówno informacje o procesach, na przykład dane narzędzi i parametry skrawania, jak i informacje o kosztach, w tym koszt pojedynczej części, wydajność godzinową i koszt inwestycji. PCA pozwala ocenić procesy w zakresie od operacji z użyciem jednej obrabiarki po pełną ścieżkę, jaką obrabiany element pokonuje w zakładzie produkcyjnym.
Koncentrujemy się na tych udoskonaleniach wydajności, które mają największy wpływ na koszty. System uwzględnia wąskie gardła i ograniczenia eksploatacyjne oraz pozwala rozpoznać obszary wymagające bardziej szczegółowych badań.
Wstępny etap analizy PCA opiera się na referencyjnym badaniu czasu i kosztów danej operacji lub zakładu. Obejmuje ocenę czynników związanych z oprzyrządowaniem, takich jak parametry procesów, czas trwania cykli i wymagania w zakresie wydajności. Etap drugi obejmuje ten sam proces, jednak wprowadzane są korekty warunków obróbki i stosowanych narzędzi. Etap trzeci może obejmować zmiany procesu, łączenie operacji i analizę bardziej rozległych zmian, takich jak modernizacja narzędzi obrabiarek.
Producenci, którzy zastosują system PCA firmy Seco, mogą bez względu na sektor działalności oczekiwać korzyści w postaci łącznych oszczędności w wysokości do 30 procent i wzrostu wydajności nawet o 40 procent.
Autor:
Patrick de Vos, menedżer ds. korporacyjnej edukacji technicznej, Seco Tools