www.przemysl-polska.com
18
'11
Written on Modified on
Produkcja opakowań szklanych dla użytku farmaceutycznego
SPAMI, spółka będąca częścią Grupy STEVANATO, opracowała system nadzoru wizyjnego w celu poprawy jakości swoich wyrobów szklanych. Kontroluje on jakość wyrobów od momentu dostawy surowca do fabryki aż do produktu finalnego. Układ składa się z systemu nadzoru wizyjnego (NoVIS), systemu ciągłego pomiaru temperatury oraz cyfrowego systemu przetwarzania obrazu o nazwie CLEANER, który jest w stanie wykryć i usunąć defekty wielkości kilku mikronów powstałe w gotowym produkcie. W pełni zintegrowany system nadzoru pozwala na pomiar średnicy rurek szklanych, grubości ich ścianek oraz temperatury przy użyciu pirometrów ( pirometryczna kontrola wyżarzania) – dzięki temu możliwe jest kompleksowe sterowanie jakością. Wykorzystanie tego systemu daje Stevanato przewagę nad innymi producentami opakowań szklanych dla branży farmaceutycznej. Dla tego zaawansowanego systemu firma SPAMI wybrała konwertery protokołów Anybus firmy HMS, umożliwiające komunikację między zdalnymi kamerami nadzorującymi a sterownikami PLC.
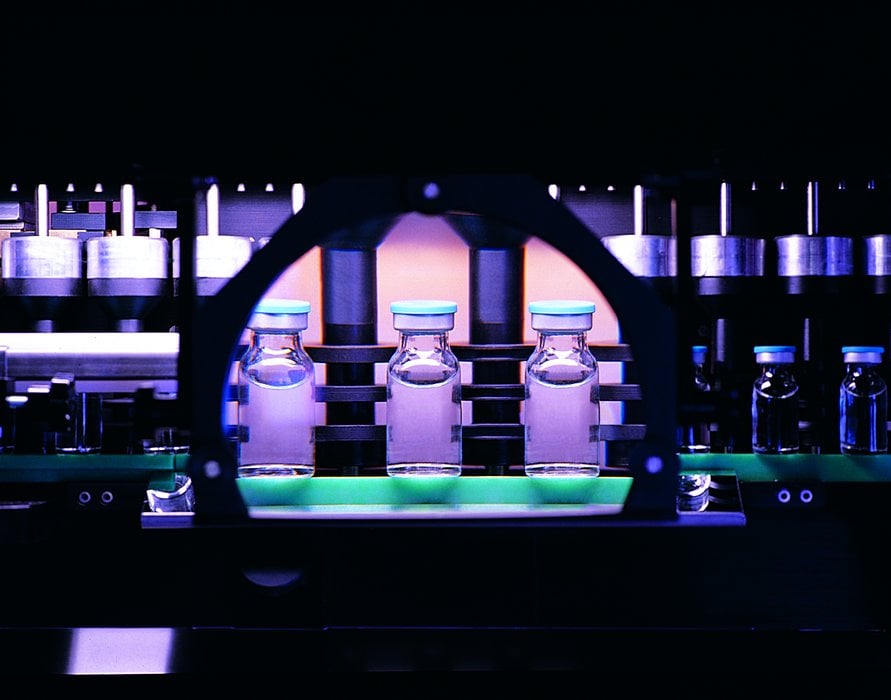
Firma została założona w 1949 roku jako warsztat rzemieślniczy w regionie słynący z bogatej tradycji wytwarzania szkła. Obecnie Grupa Stevanato jest uznanym przedsiębiorstwem przemysłowym wytwarzającym zaawansowane technologicznie produkty.
Grupa składa się z dwóch głównych oddziałów. Pierwszy specjalizuje się szczególnie w produkcji opakowań szklanych przeznaczonych do użytku farmaceutycznego. Oferuje szeroki zakres produktów - od najbardziej tradycyjnych, jak ampułki i fiolki, do coraz bardziej popularnych, jak kartridże do samodzielnych iniekcji oraz wkłady do systemów typu pen, czy gotowe do napełniania sterylne strzykawki.
Drugi oddział, tzw. inżynieryjny, złożony z firm SPAMI i Optrel, skupia się na projektowaniu i produkcji urządzeń oraz wyposażenia do inspekcji wizyjnej i monitoringu opakowań szklanych. Współdziałanie obu oddziałów zapewnia Grupie Stevanato pełną kontrolę nad całością procesu produkcyjnego: od zakupu surowców aż do wsparcia posprzedażowego.
Produkcja SPAMI jest kierowana zarówno do spółek należących do Grupy Stevanato, jak
i firm zewnętrznych. Zastosowane rozwiązania mechaniczne i elektryczne w maszynach formujących opakowania szklane zapewniają największą precyzję i doskonałą jakość gotowych produktów.
Wszystkie komponenty używane do formowania masy szklanej zostały starannie zainstalowane i sprawdzone tak, by zagwarantować dokładność wymiarów fiolek, strzykawek, kartridży i ampułek. Elementy instalowane w maszynach formujących opakowania szklane oraz na przenośnikach taśmowych zostały dobrane tak, by uniknąć ich skażenia. Cały proces produkcyjny, od załadowania rur do pakowania, jest w pełni automatyczny.
Cykl produkcyjny rozpoczyna się od rur szklanych dostarczanych w odcinkach o długości ok. 1,5 m i średnicy dobranej odpowiednio do wielkości produktu finalnego. Rura jest wprowadzana do obrotowej maszyny formującej mającej kilka głowic i zostaje podgrzana przez palniki. W zależności od wymagań procesu produkcyjnego poszczególnych produktów, w ten sposób formowane jest dno i wylot fiolek, ampułek, strzykawek itp.
Na dalszym etapie linii produkcyjnej kamery zamontowane nad przenośnikiem taśmowym dokonują dokładnego sprawdzenia opakowań szklanych – Jest to przede wszystkim precyzyjna kontrola wymiarów poprzez analizę obrazu, wyjaśnia przedstawiciel firmy, pan Gobita. Ponieważ opakowania w trakcie cyklu produkcyjnego narażone są na naprężenia mechaniczne, wyżarza się je w specjalnym piecu tzw. odprężarce, gdzie wszelkie naprężenia powstałe w trakcie formowanie wyrobu zostają usunięte. Ostatni etap cyklu to kontrola jakości gotowych produktów i zautomatyzowane pakowanie. Warto zauważyć, że ostatni etap cyklu produkcyjnego jest przeprowadzany w taki sposób, by zapewnić jakość i sterylność wymaganą w zastosowaniach farmaceutycznych.
- Istnieje wielu naszych konkurentów działających na międzynarodowym rynku. Do największych należą Niemcy i Amerykanie, ponieważ reszta firm we Włoszech jest mniejsza od naszej - wyjaśnia Gobita.
- Wartość dodana oferowana przez SPAMI to przede wszystkim jakość produktów, dzięki której wyróżniają się na tym rynku. Ponieważ nasze produkty są wykorzystywane w branży farmaceutycznej, spełniają bardzo wysokie normy jakościowe i są zgodne z rygorystycznymi wymogami ustawowymi. Wymaga to licznego i doskonale wyszkolonego personelu zajmującego się kontrolą jakości - dodaje Gobita. - Różnicę między naszą firmą a krajowymi konkurentami można dostrzec właśnie w tym aspekcie. Również możliwości badawczo- rozwojowe są naszym dużym atutem: jeśli dana firma farmaceutyczna prosi nas o produkt próbny różniący się od standardowych wyrobów, możemy go zaprojektować, ponieważ jesteśmy w stanie modyfikować i adaptować nasz system produkcyjny do konkretnych wymagań . Ta zdolność przystosowania naszych systemów produkcyjnych stanowi dużą wartość dla naszych klientów. Należy pamiętać, że w przemyśle farmaceutycznym jest wiele standardowych produktów, które wszyscy znamy, takie jak fiolki czy ampułki, ale stale wzrasta też liczba produktów specjalnych, których części są opracowywane na poczekaniu. W takich przypadkach konieczne są specjalne maszyny, które w większości są zmodyfikowanymi urządzeniami działającymi już wcześniej - konkluduje Gobita.
Owocna współpraca z HMS
Współpraca z HMS została nawiązana w celu rozwiązania specyficznego problemu komunikacyjnego. - Nasz system inspekcji został opracowany przez dział inżynieryjny w celu seryjnej kontroli jakości produktów przy wykorzystaniu nadzoru wizyjnego. Mówiąc ściślej, inteligentne kamery Cognex musiały być połączone ze sterownikami PLC firmy Siemens. Konieczne było połączenie kamer z interfejsem Ethernet ze sterownikami PLC pod kontrolą protokołu Profibus - wyjaśnia Gobita. - Po dokładnych badaniach i konsultacji z EFA Automation (wyłącznym dystrybutorem rozwiązań HMS GATEWAY we Włoszech) wybraliśmy urządzenia Anybus, które umożliwiły komunikację między naszym sprzętem - mówi Gobita.
W tym samym czasie brano pod uwagę innych potencjalnych dostawców, ale HMS było jedyną firmą mogącą zaoferować tak duży wybór konwertorów protokołów. - Ta szeroka dostępność miała kluczowe znaczenie dla dokonanego wyboru, ponieważ wiele naszych aplikacji bardzo się od siebie różni. Początkowo była istotna obsługa protokołu Profibus ze względu na sterowniki PLC firmy Siemens, niemniej jednak nasz firma normalnie wykorzystuje sterowniki programowalne różnych dostawców. Dlatego bardzo ważny dla nas jest duży wybór produktów” podkreśla Gobita. Pierwszym wykorzystanym produktem HMS było urządzenie Anybus X-Gateway konwertujące protokół Profibus na Modbus dla sieci Ethernet.
Na każdej z linii produkcyjnych może być zainstalowany więcej niż jeden konwerter Anybus. - Do tej pory wykorzystywaliśmy wiele konwerterów, ponieważ aplikacje były stosowane
w różnych systemach - kontynuuje Gobita. - Inteligentne kamery są stosowane do sprawdzania różnych aspektów jakościowych naszych produktów i muszą być zainstalowane w różnych punktach systemu. Konwertery HMS nie są dla nas wyborem jednorazowym lecz systemem, który stanie się standardem dla naszej firmy. Jesteśmy bardzo zadowoleni
z dokonanego wyboru. Produkty HMS Anybus są bardzo solidne, funkcjonalne i proste
w obsłudze w porównaniu do innych, które testowaliśmy, a przecież wiadomo, że bardzo łatwo znaleźć rozwiązania skomplikowane, a znacznie trudniej te proste - dodaje Gobita.
- Nie mieliśmy żadnych problemów z urządzeniami i wszystko wskazuje na to, że tak pozostanie. W przyszłości planujemy użycie konwerterów HMS na innych liniach produkcyjnych, gdzie oczywiście będą połączone z naszym system kontroli wizyjnej. Ponieważ standardy wymagają coraz mniejszych tolerancji, pewne jest, że zdalne systemy kontroli za pomocą kamer będą coraz popularniejsze - stwierdza Gobita.
Grupa składa się z dwóch głównych oddziałów. Pierwszy specjalizuje się szczególnie w produkcji opakowań szklanych przeznaczonych do użytku farmaceutycznego. Oferuje szeroki zakres produktów - od najbardziej tradycyjnych, jak ampułki i fiolki, do coraz bardziej popularnych, jak kartridże do samodzielnych iniekcji oraz wkłady do systemów typu pen, czy gotowe do napełniania sterylne strzykawki.
Drugi oddział, tzw. inżynieryjny, złożony z firm SPAMI i Optrel, skupia się na projektowaniu i produkcji urządzeń oraz wyposażenia do inspekcji wizyjnej i monitoringu opakowań szklanych. Współdziałanie obu oddziałów zapewnia Grupie Stevanato pełną kontrolę nad całością procesu produkcyjnego: od zakupu surowców aż do wsparcia posprzedażowego.
Produkcja SPAMI jest kierowana zarówno do spółek należących do Grupy Stevanato, jak
i firm zewnętrznych. Zastosowane rozwiązania mechaniczne i elektryczne w maszynach formujących opakowania szklane zapewniają największą precyzję i doskonałą jakość gotowych produktów.
Wszystkie komponenty używane do formowania masy szklanej zostały starannie zainstalowane i sprawdzone tak, by zagwarantować dokładność wymiarów fiolek, strzykawek, kartridży i ampułek. Elementy instalowane w maszynach formujących opakowania szklane oraz na przenośnikach taśmowych zostały dobrane tak, by uniknąć ich skażenia. Cały proces produkcyjny, od załadowania rur do pakowania, jest w pełni automatyczny.
Cykl produkcyjny rozpoczyna się od rur szklanych dostarczanych w odcinkach o długości ok. 1,5 m i średnicy dobranej odpowiednio do wielkości produktu finalnego. Rura jest wprowadzana do obrotowej maszyny formującej mającej kilka głowic i zostaje podgrzana przez palniki. W zależności od wymagań procesu produkcyjnego poszczególnych produktów, w ten sposób formowane jest dno i wylot fiolek, ampułek, strzykawek itp.
Na dalszym etapie linii produkcyjnej kamery zamontowane nad przenośnikiem taśmowym dokonują dokładnego sprawdzenia opakowań szklanych – Jest to przede wszystkim precyzyjna kontrola wymiarów poprzez analizę obrazu, wyjaśnia przedstawiciel firmy, pan Gobita. Ponieważ opakowania w trakcie cyklu produkcyjnego narażone są na naprężenia mechaniczne, wyżarza się je w specjalnym piecu tzw. odprężarce, gdzie wszelkie naprężenia powstałe w trakcie formowanie wyrobu zostają usunięte. Ostatni etap cyklu to kontrola jakości gotowych produktów i zautomatyzowane pakowanie. Warto zauważyć, że ostatni etap cyklu produkcyjnego jest przeprowadzany w taki sposób, by zapewnić jakość i sterylność wymaganą w zastosowaniach farmaceutycznych.
- Istnieje wielu naszych konkurentów działających na międzynarodowym rynku. Do największych należą Niemcy i Amerykanie, ponieważ reszta firm we Włoszech jest mniejsza od naszej - wyjaśnia Gobita.
- Wartość dodana oferowana przez SPAMI to przede wszystkim jakość produktów, dzięki której wyróżniają się na tym rynku. Ponieważ nasze produkty są wykorzystywane w branży farmaceutycznej, spełniają bardzo wysokie normy jakościowe i są zgodne z rygorystycznymi wymogami ustawowymi. Wymaga to licznego i doskonale wyszkolonego personelu zajmującego się kontrolą jakości - dodaje Gobita. - Różnicę między naszą firmą a krajowymi konkurentami można dostrzec właśnie w tym aspekcie. Również możliwości badawczo- rozwojowe są naszym dużym atutem: jeśli dana firma farmaceutyczna prosi nas o produkt próbny różniący się od standardowych wyrobów, możemy go zaprojektować, ponieważ jesteśmy w stanie modyfikować i adaptować nasz system produkcyjny do konkretnych wymagań . Ta zdolność przystosowania naszych systemów produkcyjnych stanowi dużą wartość dla naszych klientów. Należy pamiętać, że w przemyśle farmaceutycznym jest wiele standardowych produktów, które wszyscy znamy, takie jak fiolki czy ampułki, ale stale wzrasta też liczba produktów specjalnych, których części są opracowywane na poczekaniu. W takich przypadkach konieczne są specjalne maszyny, które w większości są zmodyfikowanymi urządzeniami działającymi już wcześniej - konkluduje Gobita.
Owocna współpraca z HMS
Współpraca z HMS została nawiązana w celu rozwiązania specyficznego problemu komunikacyjnego. - Nasz system inspekcji został opracowany przez dział inżynieryjny w celu seryjnej kontroli jakości produktów przy wykorzystaniu nadzoru wizyjnego. Mówiąc ściślej, inteligentne kamery Cognex musiały być połączone ze sterownikami PLC firmy Siemens. Konieczne było połączenie kamer z interfejsem Ethernet ze sterownikami PLC pod kontrolą protokołu Profibus - wyjaśnia Gobita. - Po dokładnych badaniach i konsultacji z EFA Automation (wyłącznym dystrybutorem rozwiązań HMS GATEWAY we Włoszech) wybraliśmy urządzenia Anybus, które umożliwiły komunikację między naszym sprzętem - mówi Gobita.
W tym samym czasie brano pod uwagę innych potencjalnych dostawców, ale HMS było jedyną firmą mogącą zaoferować tak duży wybór konwertorów protokołów. - Ta szeroka dostępność miała kluczowe znaczenie dla dokonanego wyboru, ponieważ wiele naszych aplikacji bardzo się od siebie różni. Początkowo była istotna obsługa protokołu Profibus ze względu na sterowniki PLC firmy Siemens, niemniej jednak nasz firma normalnie wykorzystuje sterowniki programowalne różnych dostawców. Dlatego bardzo ważny dla nas jest duży wybór produktów” podkreśla Gobita. Pierwszym wykorzystanym produktem HMS było urządzenie Anybus X-Gateway konwertujące protokół Profibus na Modbus dla sieci Ethernet.
Na każdej z linii produkcyjnych może być zainstalowany więcej niż jeden konwerter Anybus. - Do tej pory wykorzystywaliśmy wiele konwerterów, ponieważ aplikacje były stosowane
w różnych systemach - kontynuuje Gobita. - Inteligentne kamery są stosowane do sprawdzania różnych aspektów jakościowych naszych produktów i muszą być zainstalowane w różnych punktach systemu. Konwertery HMS nie są dla nas wyborem jednorazowym lecz systemem, który stanie się standardem dla naszej firmy. Jesteśmy bardzo zadowoleni
z dokonanego wyboru. Produkty HMS Anybus są bardzo solidne, funkcjonalne i proste
w obsłudze w porównaniu do innych, które testowaliśmy, a przecież wiadomo, że bardzo łatwo znaleźć rozwiązania skomplikowane, a znacznie trudniej te proste - dodaje Gobita.
- Nie mieliśmy żadnych problemów z urządzeniami i wszystko wskazuje na to, że tak pozostanie. W przyszłości planujemy użycie konwerterów HMS na innych liniach produkcyjnych, gdzie oczywiście będą połączone z naszym system kontroli wizyjnej. Ponieważ standardy wymagają coraz mniejszych tolerancji, pewne jest, że zdalne systemy kontroli za pomocą kamer będą coraz popularniejsze - stwierdza Gobita.