www.przemysl-polska.com
28
'12
Written on Modified on
Od najsłabszego ogniwa do lidera
Dlaczego nowe złącze wrzeciona maksymalizuje wydajność procesu skrawania?
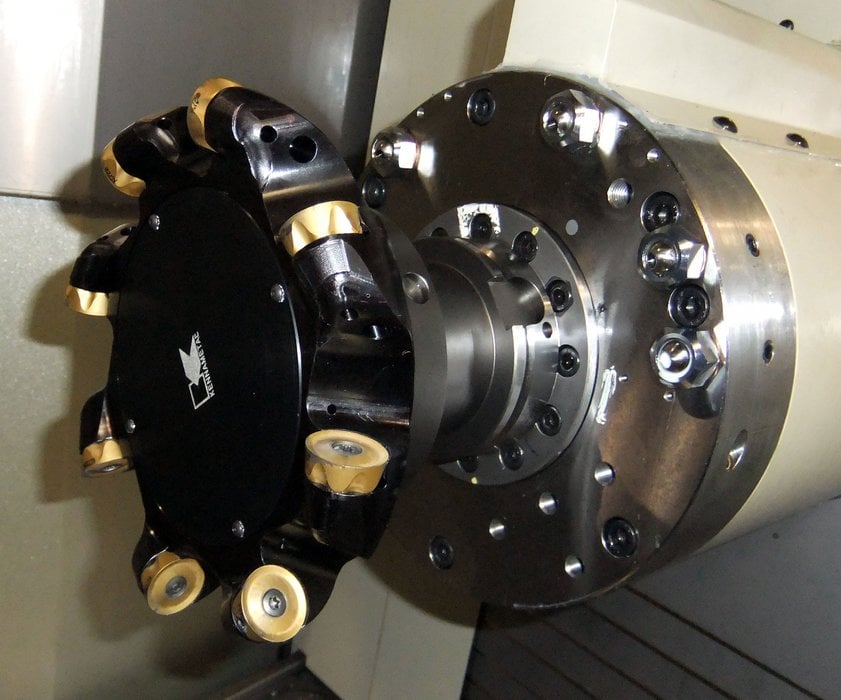
Mark Huston, wiceprezes Global Engineered Solutions
Doug Ewald, dyrektor, Global Product Management, Tooling Systems
Ruy de Frota de Souza, menedżer, Global Tooling Systems, Product Engineering
Kennametal Inc., Latrobe, PA
Obróbka wytrzymałych materiałów, takich jak tytan, jest wyzwaniem samym w sobie. Obróbka twardych stopów przy dodatkowej presji na osiąganie lepszej wydajności produkcji oznacza maksymalizację tempa usuwania metalu wobec niskich prędkości skrawania i znacznych sił skrawających. W odpowiedzi na te wyzwania konstruktorzy obrabiarek opracowali specjalne centra frezarskie i wytaczarskie cechujące się poprawioną sztywnością i tłumieniem drgań wrzeciona oraz dużych elementów maszyn. Ma to na celu ograniczenie do minimum niepożądanych wibracji pogarszających jakość obrabianych części i ograniczających żywotność narzędzi. Choć wszystkie te innowacje wpłynęły na zwiększenie wydajności, wciąż najsłabszym punktem często pozostaje samo złącze wrzeciona.
W większości przypadków połączenie wrzeciono-narzędzie determinuje, ile materiału może być usunięte w danej operacji. Jest to spowodowane tym, że złącze musi oprzeć się wysokim obciążeniom a jednocześnie utrzymać swoją sztywność dopóki odkształcenie narzędzia nie będzie zbyt duże lub nie zaczną się pojawiać drgania. Już na wczesnym etapie planowania produkcji oprócz wyboru optymalnych centrów i narzędzi skrawających warto wziąć pod uwagę takie połączenie wrzeciona, które w pełni pozwoli wykorzystać całą dostępną moc.
W ciągu ostatnich kilku dekad opracowano lub zoptymalizowano kilka typów połączeń wrzecion. Dzięki optymalnemu stosunkowi kosztów do osiąganych korzyści stożek 7/24 ISO stał się jednym z najbardziej popularnych systemów na rynku. Połączenie to sprawdziło się z powodzeniem w wielu zastosowaniach, ale ograniczenia w zakresie dokładności i wysokich prędkości uniemożliwiły mu dalszy rozwój.
Wykorzystanie powierzchni czołowej to znaczny krok naprzód w stosunku do standardowego stożka 7/24. Kombinacja powierzchni czołowej i stożka 7/24 zapewniła większą dokładność w kierunku osi Z, ale miała także wady, głównie związane z utratą sztywności przy większych prędkościach lub dużych obciążeniach bocznych. Większość narzędzi na rynku jest lita, a wrzeciona mają relatywnie małą siłę zacisku. Sztywność połączenia jest ograniczona z uwagi na konieczność minimalizowania błędów pozycjonowania. Wymagane tolerancje do uzyskania jednolitego przylegania czołowego są więc bardzo wąskie, co prowadzi do wysokich kosztów produkcji.
W 1985 r. Kennametal i Krupp WIDIA rozpoczęły wspólny program mający na celu opracowanie uniwersalnego systemu szybkiej wymiany narzędzi, znanego dziś jako KM™, który ostatnio stał się standardem ISO 26622. We wczesnych latach 90' system HSK zaczął być stosowany w maszynach w Europie, stając się normą DIN69893 a następnie ISO 12164.
KM™, system szybkiej wymiany narzędzi obrabiających, składa się z dwóch podstawowych komponentów: elementu mocującego i głowicy skrawającej. Element mocujący montowany jest na obrabiarce (głowicy rewolwerowej lub imaku narzędziowym w przypadku aplikacji stacjonarnych oraz na wrzecionie w przypadku aplikacji obrotowych) i stanowi gniazdo dla wymiennego elementu skrawającego/oprawki narzędziowej. Gdy konieczna jest wymiana narzędzia, operator łatwo zwalnia system blokujący, wymienia element obrabiający i blokuje go we właściwej pozycji – przestój maszyny jest kwestią zaledwie paru sekund.
KM4X™ firmy Kennametal to następna generacja systemu KM. Niektóre systemy narzędziowe są w stanie przenosić znaczne wartości momentu obrotowego, ale siły skrawające generują także moment zginający przekraczający limit dla połączenia wrzeciona zanim zostanie osiągnięta wartość maksymalna dla momentu obrotowego. Łącząc dużą siłę mocowania i optymalny poziom dokładności pozycjonowania, system KM4X zapewnia solidne połączenie o wyjątkowej sztywności i odporności na obciążenie zginające. Przekłada się to na znacznie większą wydajność obróbki wysoko wytrzymałych stopów i innych materiałów oraz bardzo skuteczne usuwanie metalu.
Trzykrotnie poprawiona wytrzymałość na moment zginający
Połączenie wrzeciona musi zapewniać odporność na moment obrotowy i obciążenie zginające zgodne ze specyfikacją obrabiarki i wymaganiami zwiększonej produktywności. Staje się to oczywiste w aplikacjach frezowania walcowo-czołowego, gdzie długości narzędzi są zwykle większe, a czynnikiem ograniczającym jest odporność połączenia wrzeciona na obciążenia zginające. Przykładem jest wyposażony w płytki frez o spiralnej krawędzi skrawającej, o długości 250 mm od czoła wrzeciona, mający średnicę 80mm, który generuje wartość 4620 Nm w przypadku momentu zginającego i mniej niż 900 Nm momentu obrotowego, usuwający 360 cm3/ min stopu Ti6Al4V przy RDOC 12, 7 mm i ADOC 63,5 mm.
Siła mocowania i dokładność pozycjonowania są parametrami o kluczowym znaczeniu dla stożkowo-czołowego złącza wrzeciona. Maksymalizując siłę mocowania oraz wybierając właściwe wartości wcisku można jeszcze bardziej zwiększyć sztywność połączenia.
Dzięki wykorzystaniu styku o trzech powierzchniach poprawiającego stabilność i optymalnemu rozdziałowi siły mocowania oraz dokładności mocowania, technologia KM4X™ pozwoliła osiągnąć trzykrotnie lepszą odporność na moment zginający w porównaniu do innych systemów narzędziowych.
Oznacza to, że
-warsztaty fabryczne mogą wykorzystywać wysoko wydajne obrabiarki wyposażone w system KM4X do zwiększania prędkości i posuwu w wymagających zastosowaniach obróbki, wykorzystując w ten sposób pełnię potencjału wydajności obrabiarki.
-Często mniejsze złącza KM4X takie jak KM4100 zapewniają taką samą lub lepszą wydajność niż większe połączenia.
-System KM4X może być stosowany w wielozadaniowych centrach obróbczych i wytaczarskich oraz obrabiarkach przenośnikowych w trybie ręcznym, półautomatycznym i w pełni automatycznym.
-Dzięki projektowi system KM4X może być stosowany w wielu operacjach obróbki, zarówno wymagających niskiej prędkości/wysokiego momentu obrotowego jak i dużej prędkości/małego momentu, co pozwala producentom w pełni wykorzystać potencjał maszyn.
-Operacje frezowania wiercenia i toczenia szerokiego zakresu materiałów są teraz wydajniejsze!
Wszelkie zasady i zalecenia przytaczane w tekście mają charakter ogólny. W celu uzyskania konkretnych porad dotyczących obróbki stopów tytanowych i systemu narzędziowego KM4X
prosimy o kontakt z firmą Kennametal lub odwiedzenie strony www.kennametal.com
KM4X_with_cutter.jpeg:
Łącząc dużą siłę mocowania i optymalny poziom dokładności pozycjonowania, system KM4X zapewnia solidne połączenie o wyjątkowej sztywności i odporności na obciążenie zginające. Przekłada się to na znacznie większą wydajność obróbki wysoko wytrzymałych stopów i innych materiałów oraz bardzo skuteczne usuwanie metalu.
KM4X_8.jpeg:
System złącza wrzeciona KM4X firmy Kennametal jest specjalnie skonfigurowany do pracy w warunkach wysokiej prędkości/ małego momentu obrotowego oraz niskiej prędkości/wysokiego momentu obrotowego. Bez systemu KM4X frezy o spiralnej krawędzi skrawającej przekraczałaby maksymalną wartość momentu zginającego na długo przed osiągnięciem limitu dla momentu obrotowego.
KM4X_9.jpeg:
Kombinacja siły mocowania i przylegania powierzchni poprawiły dokładność mocowania i zwiększyły trzykrotnie odporność na moment zginający w porównaniu do innych systemów narzędziowych. Zmiana narzędzia jest łatwa i szybka, a przestoje zostały ograniczone do minimum.