www.przemysl-polska.com
12
'12
Written on Modified on
Najnowsze technologie narzędziowe i rozwiązania w zakresie obróbki powierzchni zacieśniają wspólpracę pomiędzy Kennametal, a zespołem wyścigowym Ganassi
Niestandardowe myślenie podtrzymuje pasmo sukcesów
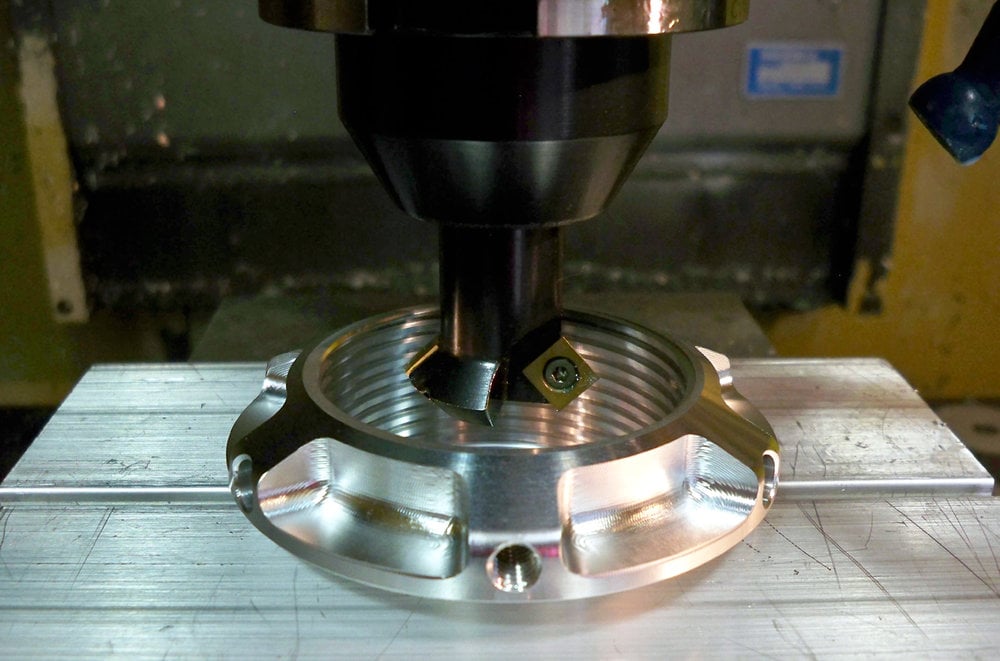
Dzięki doskonałej wydajności oprzyrządowania obróbka tytanowych komponentów w warsztacie Ganassi Indy jest tańsza niż kupno gotowych stalowych elementów od producenta.
Po ekscytującym zakończeniu wyścigu Indianapolis 500 w sezonie 2012, podczas którego Dario Franchitti i Scott Dixon zdobyli pierwsze i drugie miejsce, Chip Ganassi Racing Teams (CGRT) ogłosił długoterminowe odnowienie partnerstwa technologicznego z liderem rozwiązań inżynieryjnych Kennametal Inc.
„Jesteśmy w tym biznesie od 23 lat, a od ponad 19 lat Kennametal jest naszym partnerem” powiedział Chip Ganassi, właściciel zespołów wyścigowych Chip Ganassi Racing Teams. „W naszym warsztacie całość wyposażenia pochodzi od Kennametal, a logo firmy jest widoczne na każdym z naszych samochodów we wszystkich zespołach i seriach wyścigowych. Ale to, co czyni to partnerstwo szczególnie cennym dla naszego zespołu wyścigowego, to wiedza ekspercka Kennametal pomagająca nam funkcjonować na najwyższych obrotach również w dniu wyścigu. Kennametal podsuwa nam wiele rozwiązań dla różnych mechanicznych wyzwań z którymi się mierzymy. To wspaniale, że mamy partnera, który jest w stanie to zrobi”.
Odpowiedni ludzie, optymalne wyposażenie
Odwiedzając warsztat Target Ganassi w Indianapolis natrafimy na aktywny ośrodek w dużej mierze składający się z czterech maszyn CNC (dwu wieloosiowych centrów obróbczych oraz dwu centrów wytaczarskich, z czego jedno posiada ruchome oprzyrządowanie i przeciwwrzeciono). „Dziewięćdziesiąt dziewięć procent niezbędnych operacji obróbki wykonujemy w naszym warsztacie”, mówi John Huffman, kierownik warsztatu mechanicznego pracujący z zespołem od czternastu sezonów. Wskazuje na stalową, trójnożną osłonę wcześniej kupowaną od producenta, która obecnie wykonywana jest na miejscu ze stopu tytanu dla zwiększenia wytrzymałości i redukcji wagi. „Dzięki naszemu oprzyrządowaniu i maszynom wytwarzanie tytanowych komponentów w naszym warsztacie jest tańsze niż zakup gotowych części stalowych od producenta”, mówi . Dotyczy to również komponentów precyzyjnych o średnich wartościach tolerancji równych 0,0002 cala”.
Naturalną cechą procesu produkcyjnego w warsztacie Ganassi Indy jest jego niskonakładowość, duża różnorodność i znaczna presja czasu lub jak to ujął Huffman „wiele różnych części naraz”. Jego zespół chętnie wskazuje na różne narzędzia Kennametal zapewniające korzyści procesowe, takie jak oprzyrządowanie PCB do operacji toczenia na twardo pozwalające uzyskać precyzyjne wykończenie powierzchni bez konieczności szlifowania lub nowy, pełnowęglikowy frez HARVI II, z pięcioma rowkami wiórowymi, do zgrubnej i wykańczającej obróbki tytanu. „Nasi inżynierowie czują się pewniej przygotowując specyfikacje skomplikowanych części o bardzo wąskich tolerancjach i wysokiej jakości obróbki powierzchni, ponieważ wiedzą, że sprostamy temu wyzwaniu w naszym warsztacie'' mówi Huffman. Kennametal rozszerzył zakres swojego wieloletniego partnerstwa zapewniając zespołowi Ganassi opatentowane rozwiązanie Precision Surface Management Technology opracowane przez Kennametal Extrude Hone. Techniki wykańczania powierzchni, takie jak obróbka przetłoczno-ścierna AFM (abrasive-flow machining), ewoluowały od zwykłego usuwania zadziorów do procesów polerowania i zaokrąglania krawędzi z zachowaniem bardzo wąskich tolerancji. Dołączając do tego nowe rozwiązania w zakresie sterowania oprzyrządowaniem, charakterystyki mediów ściernych i kierowania przepływem, stale zwiększa się precyzja procesu.
Kluczowe wymagania
Obrobione otwory (także te krzyżujące się) w przypadku wielu wysokowydajnych aplikacji wymagają poprawy powierzchni - zwykle jest to intensywne polerowanie w celu osiągnięcia wymaganych tolerancji. Jakiekolwiek pozostawione drobiny metalowe lub mikropęknięcia na powierzchni powstające w procesach obróbki konwencjonalnej i niekonwencjonalnej zwiększają ryzyko obniżenia wydajności komponentów lub ich uszkodzenia. Aby wyeliminować to niebezpieczeństwo inżynierowie stosują obróbkę powierzchni AFM w konstruowaniu wielu komponentów, zwłaszcza tam, gdzie czynniki takie jak przepływ laminarny, zakłócenia w warstwie granicznej (przyściennej), resztkowe naprężenia ściskające oraz precyzyjne wykończenie krawędzi odgrywają istotną rolę. Nawet w niedostępnych obszarach uzyskano lepsze wykończenie powierzchni (chropowatość zmniejszyła się z oryginalnych 120µ cali do zaledwie16µ cali).
Maszyny AFM mogą funkcjonować jako urządzenia autonomiczne lub można je zintegrować z systemami produkcyjnymi. Standardowo, obrabiany element jest umieszczany pomiędzy dwoma przeciwstawnymi cylindrami z medium ściernym, a maszyna przetłacza medium z jednego cylindra do drugiego. Oprzyrządowanie jest «dostrojone» do charakterystyki medium ściernego (wielkości drobin oraz lepkości) w celu osiągnięcia ostatecznego poziomu wygładzenia części. Gdy medium jest przetłaczane przez ograniczoną przestrzeń jego lepkość wzrasta i to utrzymuje materiał ścierny na miejscu. Media zachowują właściwości ścierne tylko w stanie ściśniętym, więc po opuszczeniu ograniczonych przestrzeni lepkość wraca do normy i abrazja zostaje zawieszona w celu ochrony gwintów powierzchni uszczelniających.
Dalsze badania i rozwój technologii AFM przez Extrude Hone zaowocowały opracowaniem procesu MicroFlow AFM, w którym media o niższej lepkości i mniejsze drobiny ścierne umożliwiają wykańczanie i zaokrąglanie krawędzi otworów do wartości promienia 50µ cali. Dysze wtryskiwaczy paliwa mają ściśle określone promienie krawędzi umożliwiających precyzyjne rozpylanie paliwa, co przekłada się na znaczną poprawę osiągów silnika.
Huffman dodaje, że oprócz aluminium i stali stopowej coraz większy udział w pracach warsztatu ma tytan, dlatego wykorzystuje skrupulatnie liczne koncepcje zwiększające wydajność, które znajduje w katalogu „Innowacje” przeznaczonym dla przemysłu lotniczego. Należą do nich m.in. obróbka złożonych kształtów 3D czy wiertła do głębokich otworów osiągające wartość do 30 x D. „Nasze możliwości wytwarzania części we własnym warsztacie będą wzrastać ze względu na zdolność uzyskiwania coraz węższych tolerancji wymiarów części i osiągania coraz wyższej jakości wykończenia powierzchni.
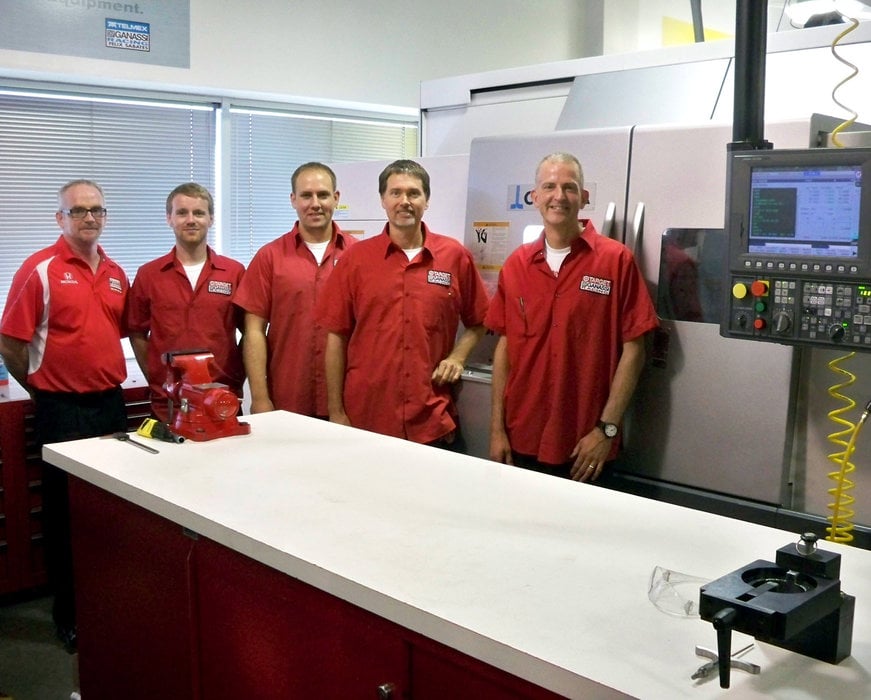
Od lewej do prawej: John Huffman, kierownik warsztatu oraz operatorzy obrabiarek Curt Sunders, Zack Robertson, Scott Stukenborg i Jay Marshall
Alphonse Girard, członek zespołu Ganassi, załadowuje maszynę Kennametal Extrude Hone
Wyścigowy bolid serii Indy w pełnej skali oraz liczne zwycięskie trofea witają gości w warsztacie Target Chip Ganassi Racing w Indianapolis.
Strefa montażowa w warsztacie Target Chip Ganassi Racing to obszar wzmożonej aktywności wielu zespołów wyścigowych.
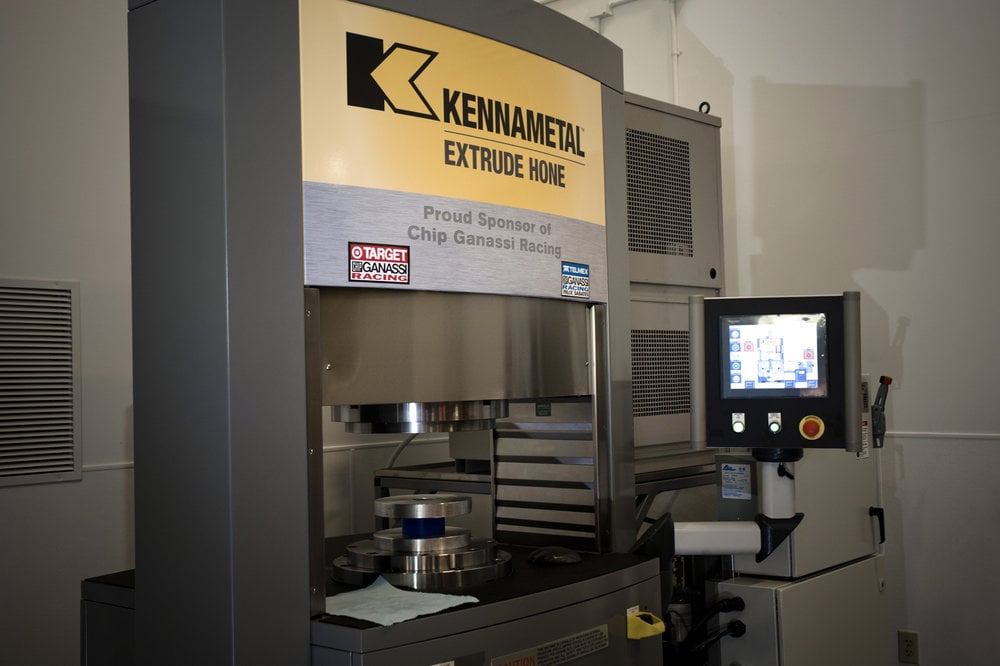
Zaawansowana technologia obróbki powierzchni pozwala poprawić wydajność wielu komponentów bolidów Indy.