www.przemysl-polska.com
06
'13
Written on Modified on
Zrównoważona optymalizacja kosztów w przemyśle motoryzacyjnym
(Forchtenberg) Redukcja kosztów jednostkowych jako metoda optymalizacji kosztów w przemyśle motoryzacyjnym nie jest wystarczająca.
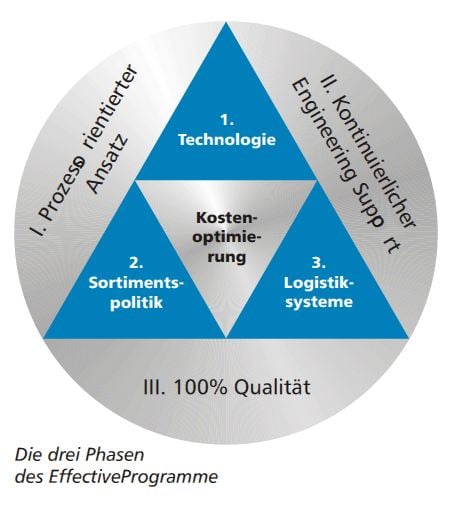
Dla poddostawców i przedsiębiorstw OEM szansą na realizację zrównoważonej optymalizacji kosztów są inteligentne koncepcje.
"Effective Programme" to przykładowa odpowiedź firmy ARNOLD Umformtechnik z Forchtenberg, specjalizującej się w produkcji elementów złącznych, na rosnącą w przemyśle motoryzacyjnym presję kosztową oraz jakościową.
Koncepcja ta opiera się na trzech filarach: innowacyjnej technologii – polegającej na redukcji kosztów związanych z realizacją projektu już na etapie fazy konstrukcyjnej tego projektu, perspektywicznej polityce asortymentowej - polegającej na ujednoliceniu programu drobnych elementów, w którym koszty jednostkowe obniżają się ze względu na większe rozmiary partii produkcyjnej oraz inteligentnym systemie logistycznym, który powinien być dopasowany indywidualnie do potrzeb każdego kontrahenta.
Fundamentalne znaczenie dla tej koncepcji mają następujące metody działania: stałe wsparcie inżynierskie, podejście zorientowane na proces już na etapie konstruowania oraz wymóg 100-procentowej jakości oferowanych części i usług (Rys.1).
- W przypadku „Effective Programme“ nie chodzi jedynie o kolejny model teoretyczny (przykład). Program ten powstał bowiem w oparciu o współpracę z naszymi dostawcami oraz firmami OEM – mówi Michael Pult, kierownik ds. marketingu i komunikacji w firmie Arnold Umformtechnik.
Dla każdego z trzech w/w filarów istnieje przedsiębiorstwo modelowe (wzorcowe), w którym skutecznie jest realizowany jeden z nich w ramach „Effective Programmes”. Współpraca tych firm doprowadziła do powstania sztandarowego modelu programu.
I tak np. poddostawca w branży motoryzacyjnej, firma Mahle, odnotowała prawie 80-procentową redukcję całkowitych kosztów produkcji dzięki zastosowaniu technologii inteligentnych połączeń oraz wczesnemu zaangażowaniu firm poddostawczych w ich własne procesy rozwojowe.
Kolejnym przykładem jest firma DaimlerChrysler, która poprzez wprowadzenie programu optymalizacji małych części (KTO) znacznie zredukowała różnorodność sprzętu. Katalog produktów tej firmy, który wcześniej zawierał 23.000 pozycji, ograniczono do ok. 12000, czyli aż o 57%.
Rezultatem jest obniżenie kosztów jednostkowych ze względu na zwiększenie rozmiarów partii. A to oznacza łatwiejszą obsługę tej znacznie ‘’odchudzonej’’ ilości sprzętu.
Arnold-Gruppe to w 100% firma córka globalnego koncernu Würth, który zatrudnia 65 000 pracowników i posiada 420 oddziałów, osiągając obrót w granicach 8 mld euro.
www.arnold-umformtechnik.de
Rys. 1 Trzy fazy „Effective Programmes”
I. Podejście zorientowane na proces
II. Stałe wsparcie inżynieryjne
III. 100-procentowa jakość
1. Innowacyjna technologia
2. Polityka asortymentowa
3. Systemy logistyczne
Kostenoptimierung – Optymalizacja kosztów