www.przemysl-polska.com
30
'21
Written on Modified on
Firma NSK opracowała ultraszybkie łożyska kulkowe dla silników pojazdów elektrycznych
Firma NSK opracowała ultraszybkie łożysko kulkowe trzeciej generacji dla silników pojazdów elektrycznych (EV), które jest w stanie pracować z wydajnością obrotową rzędu 1,8 mln dmn (1). Nowe łożysko jest obecnie najszybszym na świecie łożyskiem kulkowym poprzecznym ze smarem stałym, przeznaczonym do zastosowań w pojazdach elektrycznych, które pozwala zwiększyć zasięg pojazdu i poprawić oszczędność energii. Dodatkowo łożysko pozwala na ograniczenie wymiarów silnika i komponentów w celu uzyskania większej przestrzeni we wnętrzu pojazdu.
Zgodnie z wymogami środowiskowymi oraz oczekiwaniami konsumentów producenci samochodów poszukują mniejszych i lżejszych części samochodowych, które pozwalają zwiększyć realny zasięg osiągany przy jednym ładowaniu. Producenci OEM pojazdów elektrycznych opracowują również szybsze silniki o wyższej mocy, działające z lepszą wydajnością.W związku z tym łożyska stosowane w układach napędowych, zwłaszcza w silnikach elektrycznych, muszą spełniać wymagania odpowiednie dla coraz wyższych prędkości i osiągów.
Poprzednia (druga) generacja ultraszybkich łożysk kulkowych do silników EV osiągała wartość 1,4 mln dmn i stanowiła znaczący postęp w technologii konstrukcji koszyków łożysk oraz rozwiązań przeciwzatarciowych. Dzięki produktowi trzeciej generacji firma NSK dostosowała swoje rozwiązania do zapotrzebowania na łożyska zdolne do pracy z jeszcze wyższymi prędkościami.
Oprócz wydajności obrotowej rzędu 1,8 mln dmn (wzrost o 28,5 %) nowe łożysko posiada pierwszy na świecie koszyk, który wykorzystuje zalety techniki optymalizacji topologii. Dzięki zastosowaniu tego procesu możliwe było takie rozmieszczenie materiałów w przestrzeni projektowej, które pozwoliło zmaksymalizować wydajność produktu.
W przypadku nowej generacji łożysk optymalizacja topologii pomogła zmaksymalizować wytrzymałość i zminimalizować wagę, eliminując części, które nie poprawiały trwałości ani sztywności koszyka, a jednocześnie nową technikę wykorzystano do uzyskania kształtu koszyka zoptymalizowanego pod kątem wysokich prędkości obrotowych. Czas opracowania koszyka był bardzo krótki dzięki zastosowaniu najnowocześniejszej technologii symulacyjnej weryfikującej wydajność koszyka i kwestie produkcyjne.
W konstrukcji koszyka wykorzystano nowy materiał na bazie żywicy o wysokiej sztywności, który tłumi odkształcenia podczas szybkiego ruchu obrotowego skuteczniej niż materiały standardowe. Należy również zauważyć, że łożysko zostało wypełnione zastrzeżonym przez NSK smarem o zmniejszonej podatności na zbijanie się, co ogranicza wytwarzanie ciepła i przedłuża zarówno żywotność samego środka smarnego, jak i łożyska oraz zmniejsza ryzyko zatarcia. To właśnie połączenie specjalnego smaru NSK i nowo opracowanej konstrukcji koszyka umożliwia wysokowydajnemu łożysku kulkowemu poprzecznemu działanie przy wartości ponad 1,8 mln dmn.
Łożyska o takiej charakterystyce ułatwiają klientom opracowywanie i wdrażanie silników elektrycznych, które działają ze znacznie wyższymi prędkościami. Wyższa moc silnika przyczynia się do większej wydajności (zmniejszenia zużycia energii na jednostkę odległości), większego zasięgu pojazdu i poprawy komfortu użytkownika. Wyższe prędkości robocze ułatwiają również wykorzystanie mniejszych silników, zmniejszając w ten sposób masę pojazdu i zwiększając ilość miejsca dostępnego dla innych komponentów np. w celu instalacji większej liczby ogniw baterii lub uzyskania większego wnętrza pojazdu.
(1) dmn: Miara wydajności ruchu obrotowego łożyska. Iloczyn średnicy podziałowej łożyska (dm) i prędkości obrotowej (n).
1) Kombinacja specjalnego smaru NSK i nowo opracowanej konstrukcji koszyka umożliwia ultraszybkim łożyskom kulkowym dla silników EV działanie z wydajnością obrotową o wartości ponad 1,8 mln dmn.
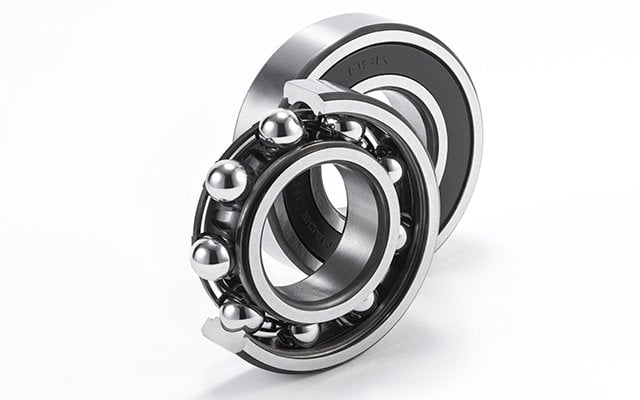
2) Etapy konstrukcyjne realizowane przez NSK w celu optymalizacji koszyka nowej generacji łożysk.
1. Problem: Potencjalne odkształcenie koszyka łożyska spowodowane siłą odśrodkową. 2. Kształt roboczy: Maksymalizacja wytrzymałości i minimalizacja ciężaru koszyka. Usunięcie części nie przyczyniających się do zwiększenia trwałości lub sztywności. 3 Ostateczny kształt: Weryfikacja wydajności i uwarunkowań produkcyjnych. Optymalna konstrukcja i łatwość wykonania.
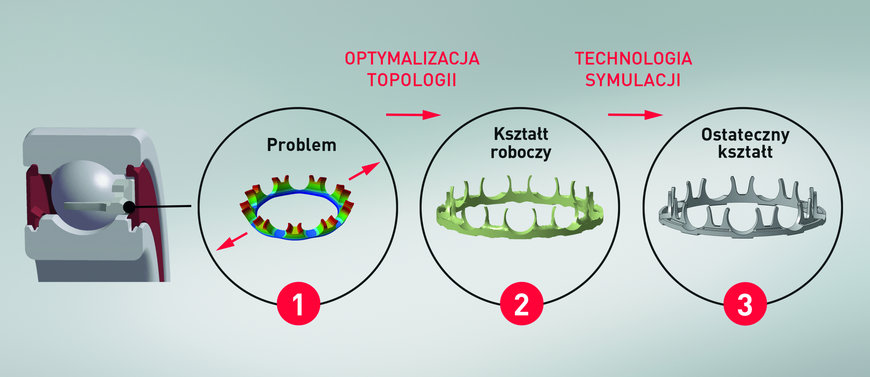