www.przemysl-polska.com
08
'16
Written on Modified on
Obróbka zgrubna ciągle bezpieczna.
Znaczenie uchwytów narzędziowych jest ciągle zaniżone, zwłaszcza kiedy mówimy o obróbce zgrubnej lub w ciężkich warunkach. Wydajność usuwania materiału w tego typu procesach jest absolutnie kluczowa dla produktywności procesu skrawania. Możliwość zastosowania specjalnych uchwytów narzędziowych wyposażonych w kamienie ustalające i narzędzia z naciętymi rowkami spiralnymi na chwycie, pozwala na pracę pełną szerokością narzędzia przy wysokim posuwie, nawet do głębokości 2xD (50 mm) lub więcej w zależności od materiału, który obrabiamy. Badania aplikacyjne przeprowadzane przez producenta obrabiarek, firmę HELLER dowiodły zasadności stosowania systemu HAIMER Safe-Lock™.
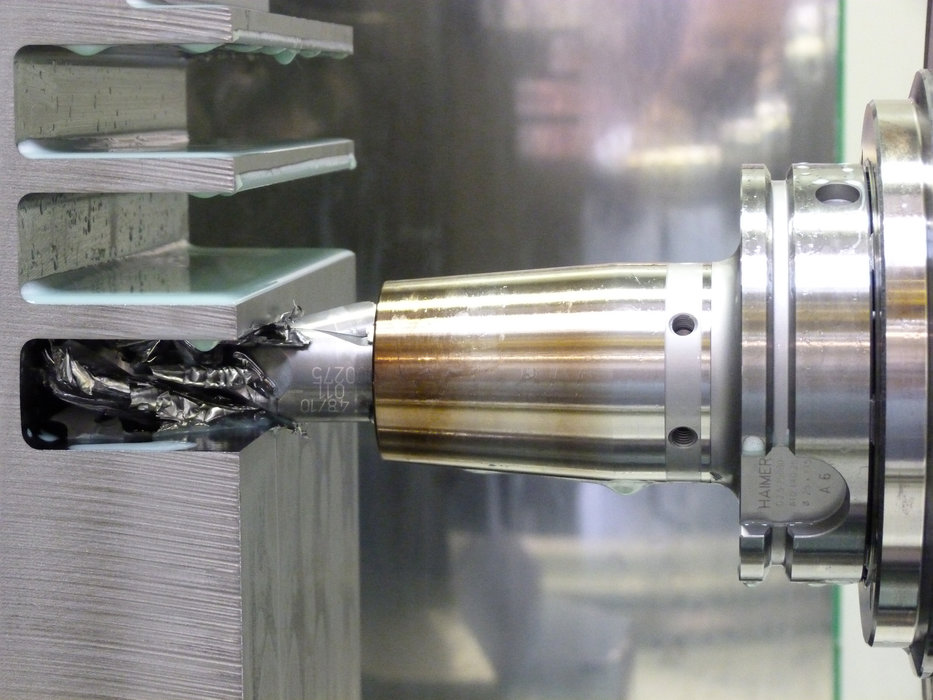
Wykorzystując uchwyty z serii HAIMER Power lub Heavy Dutywraz z systemem Safe-Lock™ możliwe jest niezawodne frezowanie przy głębokości ap = 2 x D.
Zdjęcia: Heller / Haimer
Niemal każdego dnia, osoby odpowiedzialne za produkcję, zwłaszcza w przemyśle lotniczym i energetycznym, muszą mierzyć się z zagadnieniem połączenia efektywności ekonomicznej i wysokiej niezawodności procesu. Na szczęście, wiedząc o tym, że producenci maszyn stale pracują nad rozwojem i innowacjami w zakresie technologii i tego typu problemy udaje się rozwiązywać. Obrabiarki firmy Heller znane są jako źródło inspiracji dla tego rodzaju innowacji. Firma, z siedzibą w Nuertingen w Niemczech, jest znana ze swych wysokiej jakości, 4 i 5-osiowych centrów obróbczych CNC, centrów tokarskich, maszyn do obróbki wału korbowego i wałków rozrządu wykorzystywanych w elastycznych systemach produkcyjnych. Klienci cenią sobie dostępność produktów, a takżeich kompetencje w realizacji oczekiwań klientów. Obie cechy wynikają z systemu produkcji Hellera, który opiera się na bliskiej współpracy z klientami, dostawcami i instytutami badawczymi, tak aby pozostać na czele innowacji.
Obróbka zgrubna jest procesem umożliwiającym znaczne oszczędności.
Werner Kirsten, który pracuje w dziale rozwoju technologii firmy Heller i jest odpowiedzialny za tematykę „obróbki materiałów trudnoobrabialnych”, wyjaśnia:”Nasza oferta obejmuje optymalizację procesu obróbczego wraz z naszymi klientami i dostawcami. Aby móc zaoferować tego rodzajuwsparcie, nasze centrum technologiczne wyposażone jest w różnego typu obrabiarki”. W większości przypadków celem jest podniesienie produktywności bez ryzyka związanego z niezawodnością samego procesu. Technolog Kirsten dodaje „Bardzo często osiągamy ten cel poprzez zoptymalizowanie operacji zgrubnych, co z kolei przekłada się na cały proces,dzięki skróceniu czasu operacji wykańczających. Utrzymywanie tych samych wartości technologicznych, a zarazem skrócenie głębokości cięcia o 50% skutkuje tym, że czas całego procesu zredukowany jest o połowę. Wymaga to jednak powtarzalnych i kontrolowalnych rozwiązań podczas obróbki zgrubnej”.
W związku z powyższym, aby podnieść produktywność należy uwzględnić wszystkie elementy łańcucha procesowego. Obrabiarka jest z pewnością najistotniejszym elementem całego procesu, ale nie można zapomnieć także o narzędziach, uchwytach mocujących, chłodziwie, a także innych elementach mających wpływ na powodzenie obróbki. „W końcu najsłabsze ogniwo całego procesu determinuje efekty pracy,” podkreśla Werner Kirsten. W jego opinii większość dostawców wyposażenia nie zwraca uwagi na jakość uchwytu narzędziowego, chociaż jest to szczególnie istotne dla wysokiej wydajności obróbki.”Wiele z prób, które przeprowadziliśmy w ciągu ostatnich kilku lat tego dowiodło”, wyjaśnia Werner Kirsten. Zdaliśmy sobie sprawę z tego, że oprawka ma niesamowity wpływ na proces obróbki. Na przykład, w przypadku uchwytów wzmocnionych środek ciężkości oprawki znajduje się znacznie bliżej punktu łożyskowania (ze względu na większą masę). Rezultatem tego, mamy znacznie mniej wibracji i dużo lepszą jakość powierzchni, aniżeli w przypadku użycia standardowych rozwiązań.
Mocowanie narzędzia – istotny czynnik wpływający na produktywność
Wybierając wysokiej jakości uchwyt narzędziowy możemy uzyskać znakomitą produktywność i jakość powierzchni, nawet korzystając ze standardowych narzędzi skrawających. Werner Kirsten odnosi się do badań porównawczych z podstawowymi narzędziami wyposażonych w 4 ostrza, bez możliwości doprowadzenia chłodziwa poprzez korpus narzędzia. Jako alternatywę do standardowej oprawki wybrał chwyt Haimer Power wyposażony w system Cool Flash, który to zapewnia doprowadzenie chłodziwa bezpośrednio na krawędź tnącą narzędzia. „Porównując stosowanie standardowego uchwytu termokurczliwego z uchwytem umożliwiającym doprowadzenie chłodziwa przez oprawek byliśmy w stanie uzyskać znacznie lepsze rezultaty”. Kiedy grupa przedstawicieli przemysłu lotniczego, Uniwersytetu z Dortmundu i Uniwersytetu z Hamburga odwiedziło siedzibę firmy Heller, przeprowadzono testy z użyciem tytanu Ti-6Al-4V.
Nowe spostrzeżenia w trudnych przypadkach
Dostępne było centrum 4-osiowe Heller H5000 z wrzecionem HSK – A100, gdzie moment wynosi 2290 Nm. Celem zademonstrowania potencjału i możliwości maszyny użyto do testów różnych narzędzi o średnicy 25 mm, które to miały pracować całą szerokością narzędzia, a sam test prowadzony był w tytanie. Aby zasymulować warunki stosowane w przemyśle lotniczym, narzędzia zostały zamocowane w uchwytach termokurczliwych. Przy głębokości skrawania pomiędzy 0,5 ÷ 1xD proces obróbki wydawał się bardzo powtarzalny i niezawodny. Z uwagi na to, że wrzeciono pracowało poniżej swoich możliwości, uczestnicy testu zgodzili się co do tego, że należy zwiększyć głębokość frezowania do 2xD. Werner Kirsten wyjaśnia: „Poniżej tych warunków, narzędzie wysuwa się z uchwytu podczas procesu frezowania, a w efekcie zwiększając głębokość do 2,5xD narzędzie ulega zniszczeniu wskutek narastających sił skrawania”.
Specjaliści biorący udział w testach zgodnie stwierdzili, że siła mocowania narzędzia była czynnikiem ograniczającym w tym procesie. W momencie, w którym siła osiowa i wibracje są zbyt wysokie, narzędzie wysuwa się z uchwytu w kierunku przestrzeni roboczej. W tym samym czasie siły skrawania ciągle wzrastają i dalej w efekcie narzędzie ulega uszkodzeniu, powodując również nieodwracalne zniszczenia w przestrzeni roboczej.
Przyczyny i możliwe środki zaradcze zostały omówione dość szczegółowo. W końcu Werner Kirsten rozwinął idee, że narzędzia pracują w tym samym kierunku, w którym pracuje uchwyt, a siły trzymające narzędzie są przekroczone. I w ten sposób dotarliśmy do opatentowanego przez firmę Haimer systemu Safe Lock™, który oprócz ciernych sił mocujących, ma dodatkowo wzór spirali narzędzia. Teoretycznie, system jest w stanie utrzymać narzędzie nawet gdyby oprawka straciła siłę mocowania pochodzącą od zacisku termokurczliwego.
Zapobieganie wysuwaniu narzędzia
Werner Kirsten jest w stałym kontakcie z firmą Haimer, europejskim liderze w zakresie mocowania narzędzi, w zakresie testów systemu Safe-Lock™:”Chcieliśmy być pewni, że nasze pomysły mogły zostać zrealizowane w praktyce przy użyciu rozwiązań firmy Haimer, nawet w przypadku mniej sprzyjającego środowiska”.
Firma Heller powtórzyła testy jeszcze kilkukrotnie z kilkoma zmianami. Rowki systemu HAIMER Safe-Lock™ dodawane były do kolejnych narzędzi, zmieniono także wrzeciono z HSK100 na HSK63 co obniżyło sztywność całego układu.
W rezultacie, pomimo dodatkowych czynników ograniczających, narzędzie było w stanie pracować powtarzalnie pełną szerokością z głębokością frezowania 2xD, czyli 50 mm. Werner Kirsten mówi: "W ten sposób udało nam się udowodnić zasadność stosowania system Safe-Lock™, a także to że technologia mocowania termokurczliwego ma ogromny potencjał przy współpracy z wrzecionami HSK-A100, zwłaszcza na 5 – osiowych centrach frezarskich." Później przykład ten – obróbkę tytanu Ti-6AI-4V powtórzono jeszcze kilkukrotnie, także podczas pokazów w Farnborough, gdzie udowodniono, że ograniczenie w postaci obróbki 1 x D = 25 mm może być podwojone z użyciem systemu Safe-Lock™.
Kirsten podsumowuje wyniki w następujący sposób: "Dla operacji frezowania zgrubnego jest to powtarzalny sposób. Właśnie dlatego uważam, że system HAIMER Safe-Lock™ jest praktyczny, łatwy w obsłudze i z użyciem mocowania termokurczliwego gwarantuje ogromną powtarzalność procesu, zwłaszcza w przypadku użycia standaryzowanych narzędzi innych producentów.
Liczba producentów narzędzi oferujących narzędzia z systemem Safe-Lock™
Od samego początku jego powstania, Haimer rozpoznał niesamowity potencjał Safe-Lock System ™ i to właśnie dlatego firma stworzyła program licencji, aby móc dać producentom innowacyjnych narzędzi możliwość integracji opatentowanego systemu zabezpieczającego przed wysuwaniem narzędzia z uchwytu frezarskiego. Efektem ich pracybyło stworzenie bardziej otwartego systemu mocowania narzędzi. Wiodących producentów narzędzi skrawających ma obecnie podpisane umowy licencyjne, w tym Walter, Widia, Sandvik Coromant, Seco Tools, Sumitomo, Kennametal Helical, EMUGE Franken, Danych Flet, Niagara, OSG, SGS Narzędzia i od niedawna także MAPAL.
Poprzez stały wzrost systemu Safe-Lock ™ poprzez firmę Haimer i jej licencjonowanych partnerów, system stał się nowym standardem dla ciężkiej obróbki zgrubnej. W rzeczywistości, popularność i prostota systemu Safe-Lock ™ jest taka, że można z powodzeniem zastąpić stary system Weldon, szczególnie w przypadku frezowania trochoidalnego (dynamicznego). Prezes Grupy Haimer, Andreas Haimer wyjaśnia: "Z naszym systemem Safe-Lock ™ znaleźliśmy rozwiązanie, które łączy w sobie wysoką dokładność bicia promieniowego ze 100% ochroną przed wysuwaniem narzędzia w trakcie obróbki. System z powodzeniem przyjął się jako standard w przemyśle lotniczym, a ogólnie rzecz biorąc znakomicie sprawdza się w obróbce zgrubnej i ciężkiej. Obecnie, coraz więcej firm stosuje frezowanie trochoidalne w obróbce, a to także jest badzo dobry powód do stosowania systemu Safe-Lock ™. Podczas operacji frezowaniatrochoidalnego, gdzie prędkość i głębokośćskrawaniamogą być zwiększone poprzez wsparcie oprogramowania, wydajność znacznie się poprawia. Jednak większe obciążenie krawędzi tnącej i sił skrawania pozwala uzyskać większą produktywność, a to z kolei podnosi ryzyko wysunięcia się narzędzia w trakcie obróbki. Zanim pojawił się Safe-Lock, problemy te mógły być rozwiązywne za pomocą chwytów Weldon. Klient jednak musiał ograniczyć prędkość obróbki i jej dokładność ze względu na charakter systemu mocowania. Mocowanie termokurczliwe wraz z systemem Safe-Lock ™ oferuje ten sam poziom bezpieczeństwa jak system Weldon, ale zapewnia dodatkową zaletę w postaci dokładności i wyważenia układu. Idealny poziom wyważenia i minimalne bicie w połączeniu z bezpieczeństwem wynikającym z zastosowania systemu Safe-Lock ™ pozwala osiągnąć większą wydajność poprzez szybsze dopuszczalne prędkości i zwiększoną żywotność narzędzia.
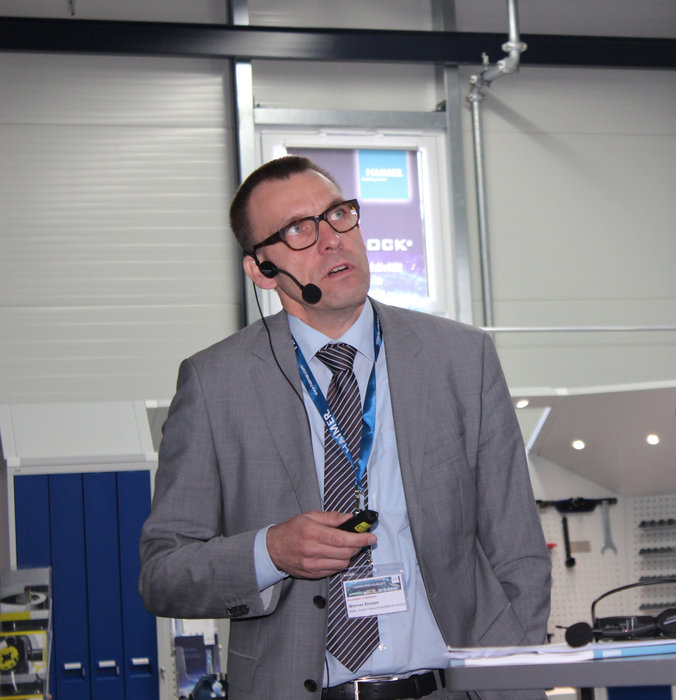
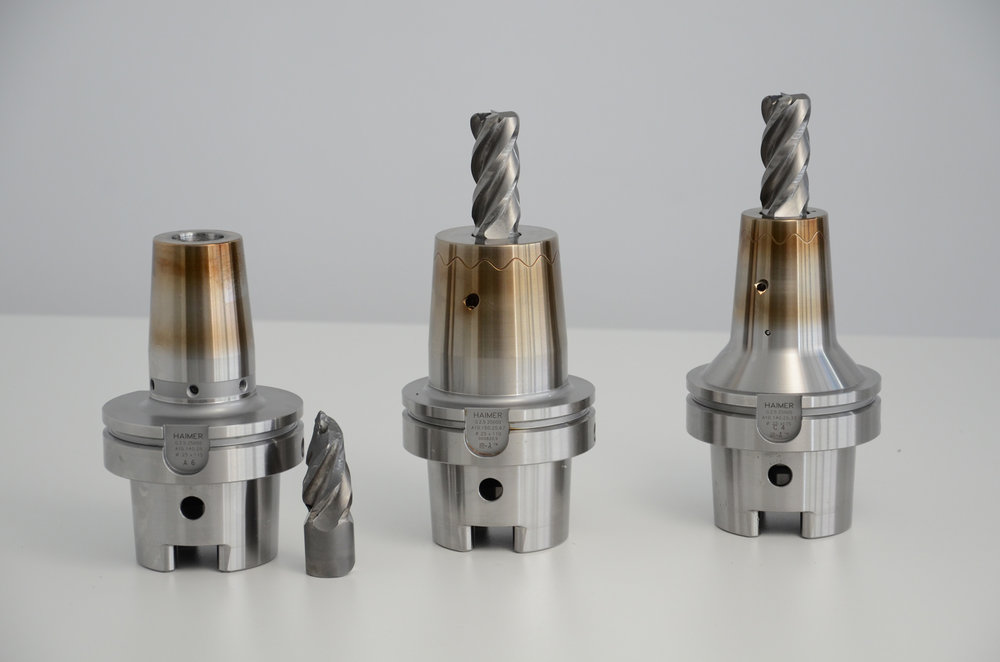
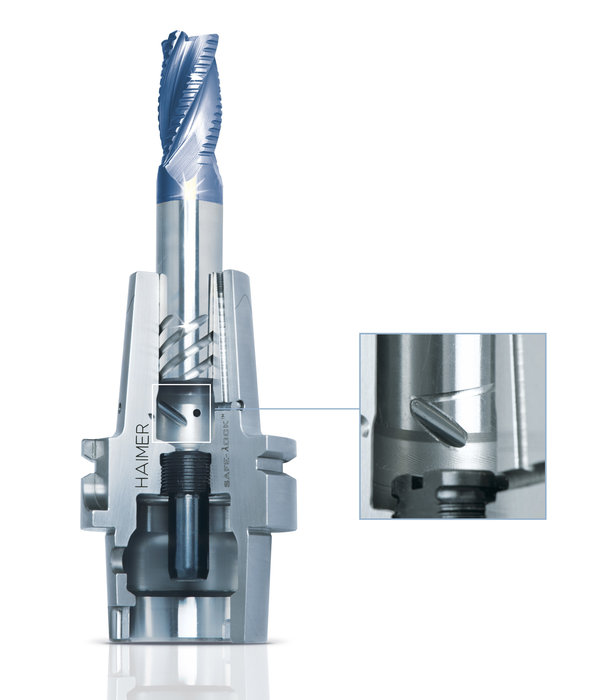
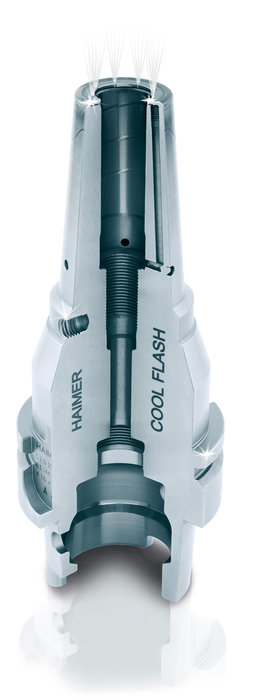
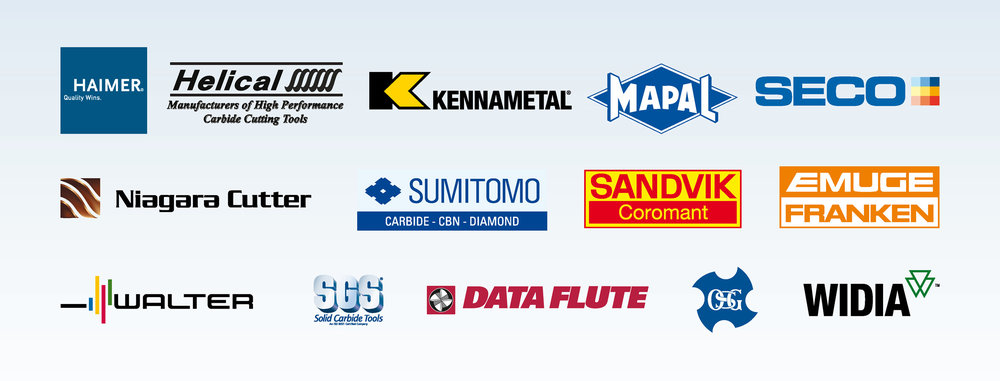