www.przemysl-polska.com
23
'10
Written on Modified on
MSR: Nowy system napędu dla stołów obrotowych
MSR znacznie upraszcza mechaniczny system przenoszenia napędu stołów obrotowych, jest także rozwiązaniem bardziej ekonomicznym od klasycznie użytkowanych.
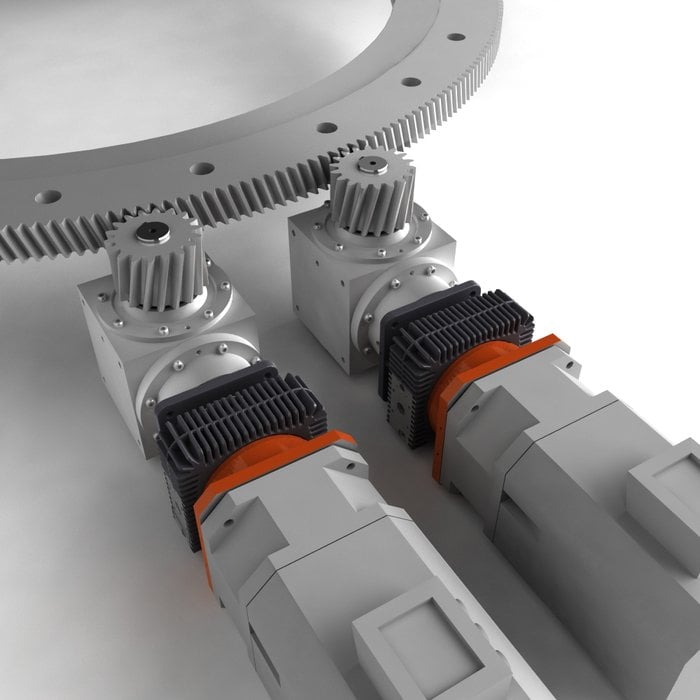
Obecnie najczęściej stosowane rozwiązanie to napęd główny ( z pojedynczym kołem zębatym) przeznaczony dla operacji toczenia i mechanizm posuwowy ( z dwoma kołami zębatymi) przeznaczony do operacji frezowania ( oś C ). Te skomplikowane i raczej drogie skrzynki przekładniowe umożliwiają dodatkowe operacje, takie jak wspomniane frezowanie.
W klasycznej konfiguracji napęd główny zapewnia całość momentu obrotowego, który jest przenoszony w sposób ciągły na stół obrotowy z wrzecionem. Napęd na ogół składa się z przekładni zębatej czołowej – dwie prędkości skrzynki przekładniowej dostosowywane są do wielkości obrabianego elementu i rozszerzają zakres przenoszonej mocy. Wysoki moment osiągany przy niskich prędkościach wykorzystywany jest do obróbki wstępnej stali lub żeliwa, natomiast wysoka prędkość pozwala na wyrównywanie i wykańczanie elementów.
Napęd osi C zapewnia całość momentu obrotowego przy niskich prędkościach dla operacji frezowania. Oba mniejsze koła zębate muszą być rozłączone w trakcie operacji toczenia, a napęd główny musi znajdować się w przełożeniu neutralnym.
REDEX ANDANTEX wprowadza rozwiązanie na rynek, które korzysta z nowego systemu napędu i sterowania ( np. Siemens CNC czy Fanuc )
Główny napęd składa się z dwóch identycznych skrzynek przekładniowych rozdzielających między sobą moment obrotowy w stosunku 50% do 50% w trakcie operacji toczenia. System CNC zarządza momentem generowanym przez silnik tak, aby wyeliminować luz. W trakcie frezowania jeden silnik napędza, natomiast drugi hamuje. Dzięki osiągniętemu w ten sposób bardzo dokładnemu pozycjonowaniu możliwe jest rozszerzenie czynności na osi C, bez żadnych dodatkowych urządzeń mechanicznych
REDEX ANDANTEX opracował dla nowego napędu rozwiązanie typu „ pod klucz”. Jest to połączenie dwubiegowego napędu MSD z przekładnią z serii R, stanowiące zintegrowany i kompaktowy system gotowy do wdrożenia. W zależności od specyfikacji, partnerzy OEM mogą używać przekładni z serii R jako opcji.
Nowa seria napędów obejmuje 4 modele MSD35R31, MSD35R41, MSD60R41, MSD60R51 charakteryzujące się wartościami momentu obrotowego od 2000/4000 Nm ( silniki 2 x 40 kW) do 9000/18000 Nm ( silniki 2 x 100 kW ) przy przełożeniu 7, 66 / 2 i 9,88 / 2.
Rozwiązanie to ( przy stosunku mniejszej zębatki do koła koronowego wynoszącym 10:15) pozwala na osiągnięcie następujących wartości:
- moment stołu obrotowego od 200 000 Nm do 270 000 Nm
- całkowite przełożenie ( skrzynka przekładniowa + koło koronowe ) 77/20 i 148/30
Rozwiązanie MSR stosowane w nowych realizacjach jest znacznie prostsze i bardziej ekonomiczne od klasycznego, w szczególności eliminuje potrzebę montażu drogich
i skomplikowanych napędów dla osi C. Już istniejące systemy również mogą skorzystać
z nowego napędu. Rozwiązanie oparte o dwa silniki jest tańsze i łatwiejsze w użytkowaniu.
W przypadku mocno wysilonego stołu obrotowego klasyczna konfiguracja składa się
z napędu o mocy 160 kW, system MSR wykorzystuje natomiast dwa silniki o mocy
80 kW każdy, które są tańsze od jednego napędu 160 kW. Dla mniejszych napędów również części zamienne są łatwiej dostępne, ponadto w przypadku osi C nie trzeba instalować tylu skomplikowanych komponentów.
W klasycznej konfiguracji napęd główny zapewnia całość momentu obrotowego, który jest przenoszony w sposób ciągły na stół obrotowy z wrzecionem. Napęd na ogół składa się z przekładni zębatej czołowej – dwie prędkości skrzynki przekładniowej dostosowywane są do wielkości obrabianego elementu i rozszerzają zakres przenoszonej mocy. Wysoki moment osiągany przy niskich prędkościach wykorzystywany jest do obróbki wstępnej stali lub żeliwa, natomiast wysoka prędkość pozwala na wyrównywanie i wykańczanie elementów.
Napęd osi C zapewnia całość momentu obrotowego przy niskich prędkościach dla operacji frezowania. Oba mniejsze koła zębate muszą być rozłączone w trakcie operacji toczenia, a napęd główny musi znajdować się w przełożeniu neutralnym.
REDEX ANDANTEX wprowadza rozwiązanie na rynek, które korzysta z nowego systemu napędu i sterowania ( np. Siemens CNC czy Fanuc )
Główny napęd składa się z dwóch identycznych skrzynek przekładniowych rozdzielających między sobą moment obrotowy w stosunku 50% do 50% w trakcie operacji toczenia. System CNC zarządza momentem generowanym przez silnik tak, aby wyeliminować luz. W trakcie frezowania jeden silnik napędza, natomiast drugi hamuje. Dzięki osiągniętemu w ten sposób bardzo dokładnemu pozycjonowaniu możliwe jest rozszerzenie czynności na osi C, bez żadnych dodatkowych urządzeń mechanicznych
REDEX ANDANTEX opracował dla nowego napędu rozwiązanie typu „ pod klucz”. Jest to połączenie dwubiegowego napędu MSD z przekładnią z serii R, stanowiące zintegrowany i kompaktowy system gotowy do wdrożenia. W zależności od specyfikacji, partnerzy OEM mogą używać przekładni z serii R jako opcji.
Nowa seria napędów obejmuje 4 modele MSD35R31, MSD35R41, MSD60R41, MSD60R51 charakteryzujące się wartościami momentu obrotowego od 2000/4000 Nm ( silniki 2 x 40 kW) do 9000/18000 Nm ( silniki 2 x 100 kW ) przy przełożeniu 7, 66 / 2 i 9,88 / 2.
Rozwiązanie to ( przy stosunku mniejszej zębatki do koła koronowego wynoszącym 10:15) pozwala na osiągnięcie następujących wartości:
- moment stołu obrotowego od 200 000 Nm do 270 000 Nm
- całkowite przełożenie ( skrzynka przekładniowa + koło koronowe ) 77/20 i 148/30
Rozwiązanie MSR stosowane w nowych realizacjach jest znacznie prostsze i bardziej ekonomiczne od klasycznego, w szczególności eliminuje potrzebę montażu drogich
i skomplikowanych napędów dla osi C. Już istniejące systemy również mogą skorzystać
z nowego napędu. Rozwiązanie oparte o dwa silniki jest tańsze i łatwiejsze w użytkowaniu.
W przypadku mocno wysilonego stołu obrotowego klasyczna konfiguracja składa się
z napędu o mocy 160 kW, system MSR wykorzystuje natomiast dwa silniki o mocy
80 kW każdy, które są tańsze od jednego napędu 160 kW. Dla mniejszych napędów również części zamienne są łatwiej dostępne, ponadto w przypadku osi C nie trzeba instalować tylu skomplikowanych komponentów.