www.przemysl-polska.com
23
'20
Written on Modified on
WIERTŁO DO KAŻDEGO Z MATERIAŁÓW
Dzięki zastosowaniu wierteł CoroDrill® 860-GM koreański producent z branży motoryzacyjnej uzyskał wzrost trwałości narzędzia o 1150%. Mówi się, że życie to nie sprint, lecz maraton. Dla producentów części samochodowych trwalsze narzędzia mają zasadnicze znaczenie dla zwiększenia rentowności produkcji, ale często nie widzą oni wystarczającego uzasadnienia dla wprowadzania zmian wyposażenia. Tutaj James Thorpe, globalny kierownik ds. produktu w firmie Sandvik Coromant, która jest światowym liderem w dziedzinie narzędzi do obróbki skrawaniem metalu, wyjaśnia, dlaczego nie należy lekceważyć znaczenia dłuższego okresu trwałości narzędzi – takich jak nowe wiertło w asortymencie CoroDrill – zwłaszcza dla zmniejszenia jednostkowego kosztu obróbki lub wzrostu ogólnej wydajności.
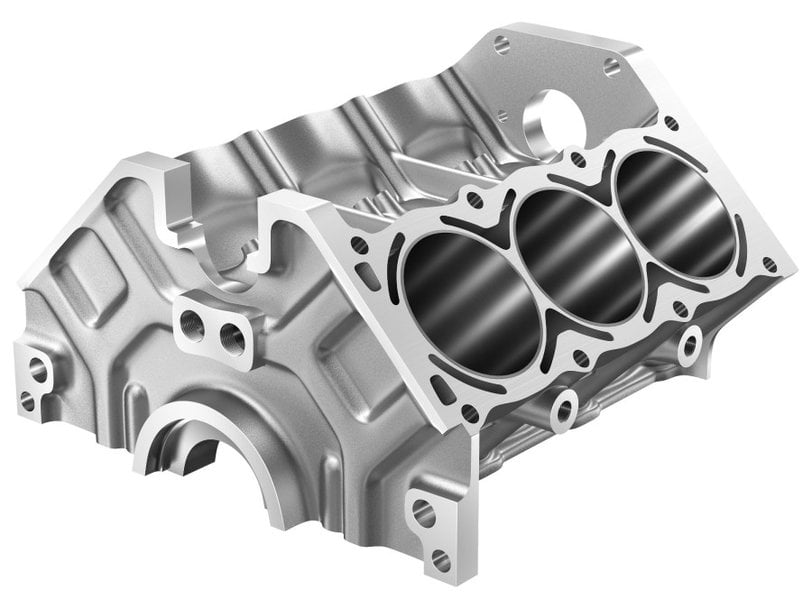
Nieprzewidywalna trwałość narzędzi to jedno z największych zagrożeń występujących w masowej produkcji motoryzacyjnej, przede wszystkim dlatego, że wiele czynności jest w znacznym stopniu zautomatyzowanych i odbywa się z wykorzystaniem najbardziej zaawansowanych systemów robotycznych i automatycznych. Przestoje są czasochłonne i zakłócają produkcję, a także sporo kosztują, dlatego nie ulega wątpliwości, że należy za wszelką cenę unikać awarii narzędzi.
W niektórych przypadkach producenci ustalają harmonogram wymian narzędzi w odstępach krótszych niż ich okres trwałości. Takie podejście jest przeważnie preferowane, ponieważ materiały używane do produkcji podzespołów motoryzacyjnych cechuje minimalna zmienność parametrów. Wynika z tego, że wymian narzędzi należy dokonywać w sposób przewidywalny, zamiast przedłużać na siłę jego eksploatację, by np. wywiercić kilka otworów więcej.
Wiercenie w różnych materiałach
Dla specjalistów z firmy Sandvik Coromant kluczem do zwiększenia żywotności narzędzia jest nie tylko czas jego użytkowania, ale także sama konstrukcja wiertła. Skutkiem takiego podejścia było stworzenie CoroDrill 860 o ulepszonej geometrii -GM – monolitycznego wiertła węglikowego o nowej konstrukcji, zoptymalizowanego pod kątem szerokiego zakresu materiałów i zastosowań we wszystkich sektorach przemysłu.
Do skonstruowania CoroDrill 860-GM firma Sandvik Coromant wykorzystała swoją specjalistyczną wiedzę z zakresu narzędzi do obróbki skrawaniem metalu, tworząc nowy gatunek o nazwie X1BM z wyjątkowym drobnoziarnistym substratem z węglików spiekanych.Drobnoziarnisty węglik charakteryzuje się większą twardością przy takiej samej udarności.
Ponadto metodą fizycznego osadzania z fazy gazowej (PVD) na wierzchołek wiertła naniesiono cienkowarstwowe pokrycie ochronne.Jest ono kluczem do zwiększenia produktywności wiertła i uzyskania przewidywalnej trwałości podczas obróbki różnorodnych materiałów. W rezultacie powstało narzędzie charakteryzujące się doskonałą stabilnością, gwarantującą wysoką niezawodność procesu obróbki i wydłużony okres trwałości podczas skrawania żeliwa, stali, stali nierdzewnej, stali hartowanych i metali nieżelaznych.
Ocena trwałości narzędzia
Lepszym sposobem oceny trwałości narzędzia jest pomiar objętości skrawanego materiału. Dla zwiększenia produktywności, w wiertle CoroDrill 860-GM zastosowano polerowane rowki wiórowe o innowacyjnej konstrukcji. Usprawniają one odprowadzanie wiórów i sprzyjają uzyskaniu otworów o wyższej jakości. Skutkuje to także ograniczeniem nagrzewania się narzędzia. Do innych zalet należy duża wytrzymałość rdzenia i mniejsze opory skrawania podczas wiercenia.
Wiertło 860-GM należy do stworzonego przez firmę Sandvik Coromant asortymentu monolitycznych wierteł węglikowych CoroDrill. Ich konstrukcja ma na celu nie tylko optymalizację wydajności, lecz także wszechstronność, co oznacza możliwość różnorodnych zastosowań do obróbki wielu materiałów w różnych branżach.
Obejmuje to zastosowanie do obróbki następujących grup materiałów: ISO-P – największa grupa materiałów w obróbce skrawaniem, obejmująca stale stopowe i niestopowe; ISO-M – obejmująca trudno skrawalne stale nierdzewne, stale austenityczne i typu duplex; ISO-K – czyli m.in. żeliwo szare, sferoidalne i ze zwartym grafitem; ISO-H – tj. stale, których twardość w skali Rockwella wynosi 45-65 HRc; oraz grupa ISO-N, do której należą bardziej miękkie materiały nieżelazne, takie jak aluminium, miedź i mosiądz.
Zaawansowana geometria
Jak już wspomnieliśmy, wiertło CoroDrill 860-GM cechuje się ulepszoną konstrukcją, ale co to właściwie oznacza? W znacznym stopniu wiąże się to z zaawansowaną optymalizacją ukształtowania wierzchołka wiertła i geometrii rowków wiórowych, umocnieniem rdzenia i zastosowaniem faz na narożach. Podwójna łysinka zwiększa stabilność podczas zagłębiania w materiał. Krawędzie skrawające poddano specjalnym zabiegom obróbki wykończeniowej w celu usunięcia mikrouszkodzeń. Na wierzchołku wiertła uzyskano lepsze kąty przyłożenia i wyższą jakość powierzchni.
Właściwości te przyczyniają się do stabilizacji wiertła, ograniczenia powstawania zadziorów na wejściu i na wyjściu ostrzy z materiału oraz zapewniają lepszą klasę dokładności wymiarowej, jakość wykończenia i prostoliniowość wierconych otworów. Wiertło to odznacza się także miarowym postępem zużycia i doskonałą precyzją wykonania otworów.
Większa trwałość
Dla producentów z branży motoryzacyjnej wiertło CoroDrill® 860-GM okazało się przydatnym narzędziem do wiercenia otworów w blokach silnika, obudowach, pierścieniach i kolektorach. Jednak oprócz przemysłu motoryzacyjnego i maszynowego wiertło nadaje się także do wielu innych zastosowań, w których jakość otworu ma krytyczne znaczenie, takich jak branża lotnicza, przemysł wydobywczy ropy naftowej i gazu, energetyka atomowa i branża odnawialnych źródeł energii.
Wśród najbardziej imponujących rezultatów, jakie udało się dotychczas uzyskać dzięki 860-GM, są wyniki osiągnięte przez koreańskiego producenta części samochodowych. Obróbka u klienta polegała na wierceniu otworów w produkowanej partii elementów łączących do układu przeniesienia napędu. W każdym przedmiocie wiercono ogółem osiem otworów o średnicy 8,2 mm na głębokość 10 mm.
Stosowane wcześniej wiertło starczało na wyprodukowanie 200 przedmiotów, czyli w sumie 1600 otworów, przy prędkości skrawania Vc=80 m/min (tj. 3102 obr./min) i prędkości posuwu Vf=381 mm/min. Natomiast wiertło CoroDrill 860-GM umożliwia wyprodukowanie aż 2300 przedmiotów (18400 otworów) z prędkością skrawania Vc=100 m/min (tj. 3878 obr./min) i prędkością posuwu Vf=814 mm/min. W efekcie odnotowano znaczne zwiększenie okresu trwałości narzędzia o 1150% oraz wzrost produktywności, który istotnie przyczynił się do obniżenia jednostkowego kosztu obróbki. O zbliżonych imponujących wynikach informują inni klienci Sandvik Coromant z branży motoryzacyjnej na całym świecie.
Solidny wybór
Potencjał wiertła CoroDrill 860-GM to nie tylko bezpieczeństwo procesu obróbki i większa trwałość narzędzia. Ponieważ wiertło umożliwia obróbkę wszystkich materiałów, można zmniejszyć zapasy magazynowe i uzyskać większą elastyczność eksploatacji obrabiarek, czego skutkiem jest skrócenie czasu ustawiania i redukcja kosztów. Zalety te świadczą o tym, że producenci z branży motoryzacyjnej powinni rozważyć pozytywny wpływ zastosowania ulepszonych wierteł, takich jak 860-GM, na końcowy bilans, zwłaszcza w kontekście długoterminowych korzyści – bo życie to nie sprint, lecz maraton.
www.sandvik.coromant.com